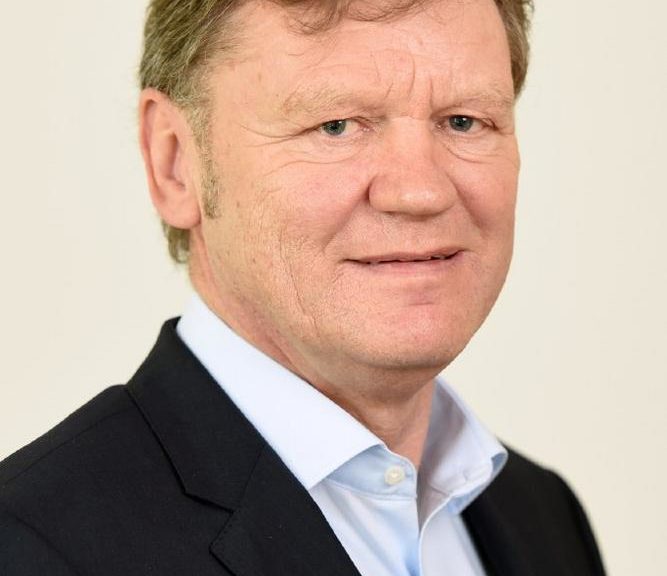
WEDDERHOFF IT mit umsatzstärkstem Geschäftsjahr seit Gründung
„Das Geschäftsjahr 2017 ist für uns sehr positiv verlaufen. Wir haben sämtliche Zielvorgaben erreicht und das umsatzstärkste Jahr seit unserer Gründung verzeichnet“, bilanziert Peter Wedderhoff, Geschäftsführer der WEDDERHOFF IT GmbH. Insgesamt hat der Softwarehersteller 14 Neukunden im Fahrzeug- und Maschinenbau gewonnen und seinen Umsatz um 6 Prozent gesteigert.
Für 2018 plant WEDDERHOFF, seine Aktivitäten im Geschäftsbereich Maschinenbau auszubauen und seine Erfahrungen aus dem Fahrzeugbau auf dieses Segment zu übertragen. Zudem treibt der Software- und Beratungsspezialist in diesem Bereich die Implementierung seines ERP-Systems WIAS enterprise voran. Die neuste Version der modularen Softwarelösung ist speziell auf die Anforderungen im Maschinenbau zugeschnitten und bildet alle produktionstechnischen und betriebswirtschaftlichen Kennzahlen zur Steuerung der internen Unternehmensprozesse ab. Auch der Vertrieb der Dokumenten-Management-Software „DocuWare“ vor allem bei kleinen und mittelständischen Unternehmen aus der Region soll verstärkt werden.
Darüber hinaus ist für dieses Jahr geplant, die Prozesse der WEDDERHOFF IT GmbH und der WEDDERHOFF Beratungs- und Vertriebs GmbH & Co. KG (WBV) enger miteinander zu verzahnen. Aufgrund seiner Branchenexpertise und der hohen Zahl erfolgreich durchgeführter Projekte ist der Softwareentwickler auch in der Lage, vielfältige Beratungsleistungen für das produzierende Gewerbe zu erbringen. Neben der Aggregation von Daten fasst WEDDERHOFF unter diesen Punkt vor allem die Interpretation der Daten, die über WIAS gewonnen werden: „Wir entwickeln und vertreiben nicht nur hochentwickelte Software, sondern bieten unseren Kunden darüber hinaus auch eine ganzheitliche Beratung. Als Ingenieure gehen wir dabei pragmatisch und lösungsorientiert vor“, sagt Peter Wedderhoff.
Die WEDDERHOFF IT GmbH agiert als innovatives Softwareunternehmen seit 1994 in Deutschland, Österreich und der Schweiz. Die ERP-Systeme des Unternehmens für die Serien-, Varianten- und Sonderfertigung sind heute in den Bereichen Karosserie- und Fahrzeugbau, Maschinen- und Anlagenbau, Lohnfertigung sowie in der Agrar- und Kommunaltechnik führend. Wichtigstes Produkt im umfangreichen Leistungsspektrum des Software- und Beratungsspezialisten ist das modulare ERP-System WIAS (Wedderhoff Integrierte Auftrags Steuerung). WIAS umfasst sämtliche Betriebsabläufe von der Auftragsabwicklung bis hin zur Betriebsdatenerfassung. Gleichzeitig werden mit über das Programm wichtige Kennzahlen für das Management – zum Beispiel zur Produktivität – erzeugt. Das System wird in unterschiedlichen Versionen, abhängig von der Unternehmensgröße, angeboten und stetig praxisorientiert weiterentwickelt. Abgerundet wird das Portfolio durch zahlreiche Erweiterungen, Dienstleistungen wie Produktschulungen oder Organisationsberatungen für Unternehmen. Am Sitz in Mettingen/Westfalen beschäftigt WEDDERHOFF derzeit 24 erfahrene Berater und Software-Spezialisten.
Wedderhoff IT GmbH
Bischofstraße 3a
49497 Mettingen
Telefon: +49 (5453) 50562-300
Telefax: +49 (5452) 50562-25
http://www.wias.de
Telefon: +49 (251) 625561-14
Vertriebsleiter
Telefon: +49 (5452) 50562-410
Fax: +49 (5452) 50562-25
E-Mail: roeber@wias.de
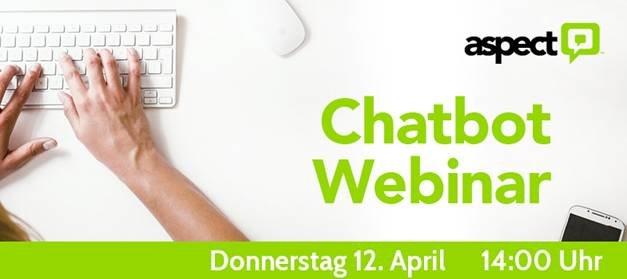
Aspect Webinar: Mit Chatbots Services ohne Warteschleife realisieren – Optionen zur Einführung von Chatbots im Contact Center Gesamtsystem
Am Donnerstag, den 12. April geht es um Chatbots: Marketing Resultant Harald Henn und Tobias Göbel, Senior Director Emerging Technologies bei Aspect Software, sprechen darüber, wie mithilfe von Chatbots positive Serviceerlebnisse realisiert werden können. Die beiden Referenten geben einen Überblick zur Strategie und Planung von Chatbot-Einführungen und zeigen u.a. auf, wie ein Anliegen im Erstkontakt geklärt wird bzw. wie eine Chatbot- oder Messenger-Anfrage in den Live-Support eskaliert werden kann, ohne dass der Kunde sein Anliegen wiederholen muss.
Die Teilnahme ist kostenfrei, eine vorherige Registrierung ist erforderlich.
- Donnerstag, 12. April, 14:00 Uhr: „Mit Chatbots Services ohne Warteschleife realisieren“. Weitere Informationen und Anmeldung
Aspect Software GmbH
Von-der-Wettern-Str. 27
51149 Köln
Telefon: +49 (6102) 3050000
Telefax: +49 (2203) 9883860
http://www.aspect.com
Telefon: +49 (228) 926 83 300
Fax: +49 (228) 926 83 333
E-Mail: aspect@pragma-pr.de
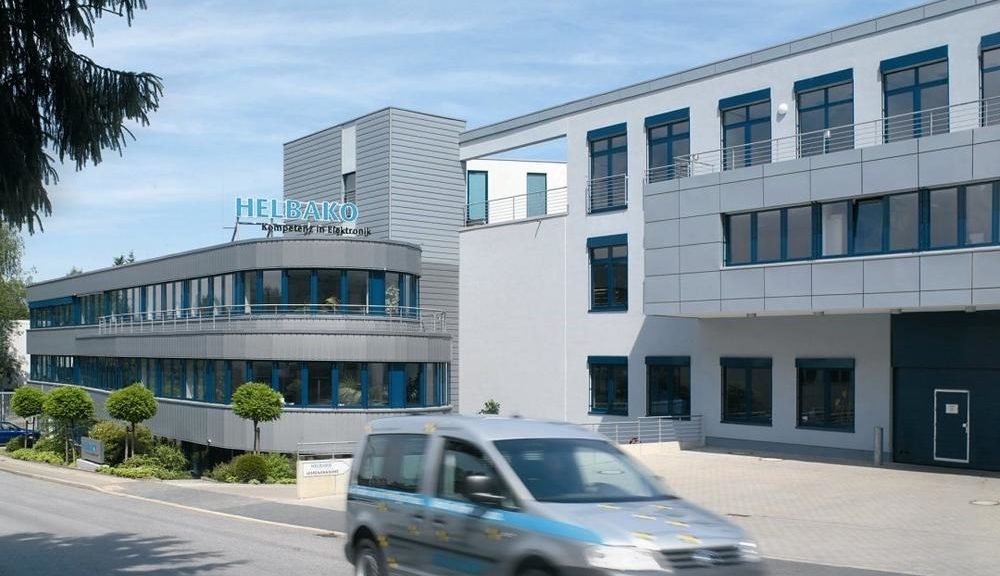
Interview mit Ralf Diepers (RD) und Andreas Schneider (AS)
Im eigenen Entwicklungszentrum mit über 60 Mitarbeitern werden Produkte für unterschiedliche Bereiche am PKW entwickelt. In Heiligenhaus werden die eigenen Produkte entwickelt und hergestellt. Als EMS Dienstleistung werden in kleinem Masse auch Produkte anderer Unternehmen hergestellt.
Die gesamte Organisation ist deshalb zwingend an den für Automobilzulieferer vorgegebenen strengen Erfordernissen (TS16949) ausgerichtet. Prozessorientiertes Denken und das Streben nach kontinuierlicher Verbesserung sind dabei prägend für die Unternehmenskultur geworden.
Eine durchdachte Planung und ein konsequentes Controlling sind dabei wesentliche Stützen des beachtlichen und kontinuierlichen Erfolg des Unternehmens. Die Anlagenproduktivität liegt dabei besonders im Fokus.
Verstecktes Potential
RC: Herr Diepers, was hat Sie auf die Idee gebracht, Produktionsdaten automatisiert zu ermitteln?
RD: Wir wussten, dass bei der Anlagenproduktivität ein noch ungenutztes Potential liegt, dies konnte unser Produktionscontrolling eindeutig nachweisen. Für mich als Leiter der Fertigung stellte sich die Frage, wie ich dieses Potential möglichst schnell identifizieren und heben konnte. Übliche Verbesserungsmöglichkeiten wie z.Bsp. Wartungs- oder Rüstoptimierungen wurden zwar durchgeführt, deren Nachhaltigkeit war jedoch nur über aufwändige Zeitstudien und Analysen nachzuweisen.
Da wir im Dreischichtbetrieb arbeiten war mir klar, dass wir nur dann weitere Produktivitätssteigerung erzielen können, wenn wir eine automatisierte Datenermittlung und Auswertung durchführen. Einzelne Anlagen in unserem SMD Bereich verfügten bereits über Möglichkeiten zur Datenanalyse, allerdings waren die Auswirkungen von Störungen oder Optimierungen einzelner Anlagen auf die Gesamtverfügbarkeit der SMT-Linie nicht immer nachvollziehbar.
Mit den bisherigen Auswertungen konnten wir die uns gesteckten Produktivitätsziele nicht erreichen.
Suche
RC: Wie kamen Sie denn in diesem Zusammenhang auf Promatix?
RD: Bei der Suche nach einer geeigneten Lösung schaute ich mir auf einer Messe das Promatix System „Linealyzer“ an. Dargestellt wurde die Auswertung eine SMD Linie die quasi unserer Linienkonfiguration entsprach. Interessant war, dass das System universell verwendbar ist – sowohl für SMD Linien als auch für andere Anlagen. Da wir sowohl SMD Linien als auch automatisierte Systeme im Backendbereich analysieren wollten, konnten wir diese mit einem einheitlichen System ausstatten. Konkret 3 SMD Linien und 2 Anlagen im Backendbereich.
Obwohl die Anforderungen an ein Produktionsdatenerfassungssystem je nach Anwender sehr unterschiedlich sind – von der „Managementübersicht“ bis hin zur „Detailanalyse einzelner Linienstörungen“- sollten diese in einem System realisierbar sein.
Während der Präsentation möglicher Systemauswertungen zeigte sich schnell, dass diese Anforderungen über Promatix realisierbar sind incl. der Anbindung an unser SAP System um die Sollwerte für die Linienleistung zu übernehmen. Auswertungen von Detaildaten wie Rüstzeiten, Störungsgründe und Ähnliches sind auf Knopfdruck verfügbar, so dass aufwendige Zeitstudien und Analysen der Vergangenheit angehören.
Das System bietet somit die Grundlage für schnelle zielgerichtete Analysen zur Produktionsoptimierung.
RC: Sie optimieren also ihre Produktion mit dem Linealyzer?
RD: Ja, das System hat alle Funktionen, die für systematische Analysen und ein Shopfloormanagement erforderlich sind.
Seit 2014 optimieren wir unsere Fertigung mit Lean Ansätzen. Wesentliche Punkte für ein erfolgreiches Lean Management sind die Verringerung von Durchlaufzeiten und die Erhöhungen von Anlagennutzungsgraden.
Das Reporting System von Promatix stellte uns im Lean Projekt die wesentlichen Informationen zur Verfügung um an der richtigen Stelle zu optimieren. Hierbei wurden sowohl technische Störungsgründe als auch organisatorische Themen durch gezielte Datenauswertung aufgezeigt. Nach der Umsetzung von Optimierungen sind die Auswirkungen über das System umgehend erkennbar und auch die Nachhaltigkeit kann kontinuierlich verfolgt werden.
Gerade in Bezug auf die Detailanalysen bei eventuell wieder auftretenden Abweichungen ist das System bei uns zu einem Standardwerkzeug für die Führungskräfte und Produktionsmitarbeiter geworden.
Ich persönlich werde einmal wöchentlich von Hr. Schneider –dem für den SMT Bereich verantwortlichen Gruppenleiter- über die aufgetretenen Probleme und geplanten Abstellmaßnahmen informiert.
RC: Herr Schneider, wie kam das System denn bei Ihren Mitarbeitern an?
AS: Für mich war es von Anfang an wichtig, dass die Mitarbeiter nicht mit zusätzlicher Arbeit belastet werden, die Fehlerkommentierung sollte schnell gehen, und einfach sein.
Dies war durch die Struktur der Bedienoberfläche und des Auswahlmenues gegeben.
Da die Kommentierung der Stillstandszeiten bisher händisch erfolgte, konnte ich an dieser Stelle sogar eine Arbeitserleichterung feststellen.
Durch den Online Monitor über den SMD Linien sind die Kolleginnen und Kollegen immer über den aktuellen Stand der Schicht informiert. Dies hatte bei uns zur Folge, dass das Team aktiv an dem Projekt mitarbeitete, und die Motivation für Verbesserungsvorschläge zugenommen hat.
RC: Herr Schneider, unterstütz Sie das System im Alltag?
AS: Mein Arbeitstag beginnt damit, dass ich mir eine Auswertung aus dem Promatix System über die vergangenen 3 Schichten erstelle. Ich überprüfe den Nutzungsgrad und halte nach Planabweichungen Ausschau. Es geht mir dabei um die 3 größten oder wiederholten ungeplanten Unterbrechungen pro Schicht und deren Ursachen. Auffälligkeiten bespreche ich dann mit meinen Teamleitern.
Bei unserer Shopfloor Managementrunde mit Fertigungs- und Gruppenleiter geht es überwiegend um Themen, welche die Linienausnutzungsgrade steigern sollen. Wir finden mit dem System Linealyzer auf einfache Weise Optimierungspotentiale und kontrollieren damit auch ob die angesetzten Verbesserungen zum Erfolg führten.
Gerade aber auch kleinere Produktionsunterbrechungen, welche in der Vergangenheit nicht dokumentiert wurden, ließen sich mit Hilfe des Linealysers ermitteln.
Uns ist zum Beispiel in den letzten Tagen aufgefallen, dass an einer unserer Linien sporadisch gegen 12.00 h nachts, eine Unterbrechung verursacht durch den Reflow Ofen, entstand. Produktionsunterbrechung < 5min.
Unsere Kollegen der Nachtschicht hatten kommentiert, die Ursache sei eine nicht ausreichende Stickstoffversorgung gewesen. Wir setzten umgehend ein Team zur Fehleranalyse an und konnten innerhalb weniger Tage die Ursache beheben. Wir kontrollieren mit dem Linealyzer nachfolgend, ob der Fehler wieder auftritt, bzw ob unsere durchgeführten Maßnahmen die gewünschte Wirkung zeigen. Ich bin mir sicher, ohne den Linealyzer wäre dieses Phänomen nicht aufgefallen. Dies ist nur 1 Beispiel von vielen.
RC: Sie arbeiten also täglich mit dem System?
Ja, absolut! Natürlich arbeite ich mit dem System täglich, und meine Mitarbeiter auch.
An meinem Arbeitsplatz, und am Arbeitsplatz meiner Teamleiter befindet sich ein Cockpit, das immer den Status der einzelnen Anlage aufzeigt, es sind die Informationen, die auch direkt an der Anlage auf dem Online Monitor den Mitarbeitern zur Verfügung stehen.
Am Anfang, als wir das System eingesetzt hatten, hatte ich die Mitarbeiter an der Anlage angerufen, oder bin direkt hingegangen, wenn eine Unterbrechung mir als zu lange erschien.
Heute ist dies nicht mehr erforderlich, ich bekommen einen Anruf, in dem erklärt wird, was geschehen ist, und was unternommen wird, diesen Zustand schnell zu ändern.
Wir brauchen heute nicht mehr zu diskutieren, ob ein Problem tatsächlich existiert, dies wird uns als Tatsache von dem System mitgeteilt. Wir verwenden unsere Energie dafür, die erforderlichen Dinge systematisch anzugehen und nachhaltig zu lösen.
Das Promatixsystem verhalf uns unbekannte Störgrößen aufzudecken und Verbesserungspotenziale zu ermitteln. Durch die Eliminierung dieser Stillstandzeiten, erreichten wir eine Steigerung der Liniennutzungrade um 26%.
Papierlos
RC: Wenn ich das richtig verstehe, unterstütz das System sowohl das Management als auch die Mitarbeiter in der Produktion?
AS: Das kann man so sagen. Es geht ja auch nur gemeinsam. Wenn die Mitarbeiter keine Mitgestaltungmöglichkeit und keine Vorteile hätten, wäre es ein reines Kontrollsystem. Es würde dann zwar die Leistung anzeigen, aber das wäre dann auch alles. Die Frage, wie diese verbessert werden kann, würde offen bleiben.
Seit unser Schichtbericht auf dem Linealyzer System läuft, arbeiten wir in unserem Bereich papierlos. Das hat den Vorteil, dass die Informationen digital abgelegt sind, mit schneller Zugriffsmöglichkeit. Für die Mitarbeiter bedeutet es eine zeitliche Entlastung, da nur noch Kommentare für außergewöhnliche Ereignisse zu berichten sind, die wesentlichen Angaben sind automatisch von dem System ermittelt.
Promatix hat den Bericht exakt nach unseren Angaben umgesetzt, es war im Grunde ein Gemeinschaftsprojekt.
Rüstprozess
RC: Was zeigt das System an, wenn Sie Umrüsten?
AS: Bedingt durch unsere Auftragsstruktur sind bei uns pro Schicht manchmal mehrere Rüstvorgänge erforderlich. Während des Rüstvorgangs zeigt der Online Monitor die Linie in gelber Farbe an, so dass der Status „Rüsten“ erkennbar ist. Ein Hauptansatz im Leanprojekt war, diese Rüstzeit drastisch zu reduzieren. Der Linealyzer zeigt die Rüstzeit an und zeichnet sie automatisch auf. Dies half uns bei der Ermittlung realer Rüstzeiten.
Außerdem können wir unmittelbar nachhalten, ob unsere Bemühungen um eine Rüstoptimierung erfolgreich sind. Wiederholte Rüstzeitanalysen zwischen der theoretisch ermittelten und realen Rüstzeit sind problemlos und ohne weiteres Personal durchführbar.
Überblick / Kennzahlen
RC: Das hört sich so an, dass Sie immer damit arbeiten, wenn etwas nicht klappt wie geplant?
AS: Wenn Sie das so sehen – ja, immer wenn eine Kennzahl vom Plan abweicht, wollen wir wissen warum, dafür haben wir das System. Es hilft uns, schnell besser zu werden, mit der notwendigen Transparenz.
Mit der Cockpitfunktion habe ich alle wesentlichen Informationen auf einem Bildschirm, und kann den jederzeit über mein Smartphone einsehen, egal wo ich bin (Empfang vorausgesetzt) und egal um welche Zeit. Diese Funktion nutze ich seit bereits 3 Jahren.
RC: Ich bedanke mich für Ihre Ausführungen!
Promatix GmbH
Uhlmannstrasse 45
88471 Laupheim
Telefon: +49 (7392) 70916-38
http://www.promatix.de
Geschäftsführer
Telefon: +49 (7392) 709-1638
E-Mail: hubert.schoenle@promatix.de

Anlagenproduktivität im Fokus
Helbako ist ein mittelständischer Automobilzulieferer mit Hauptsitz in Heiligenhaus. Mit etwa 260 Mitarbeitern produziert das Familienunternehmen hier jährlich 5 Mio. elektronische Steuerungsmodule. Seit 2015 wird auch am chinesischen Fertigungsstandort in Ningbo produziert und für den europäischen Markt befindet sich ein neuer Entwicklungs- und Fertigungsstandort in Osteuropa in der Umsetzung. Im eigenen Entwicklungszentrum mit über 60 Mitarbeitern entstehen Produkte für unterschiedliche Bereiche am Personenkraftfahrzeug. Als EMS-Dienstleistung werden in kleinem Maße auch Produkte anderer Unternehmen hergestellt. Die gesamte Organisation ist deshalb zwingend an den für Automobilzulieferer vorgegebenen strengen Erfordernissen (TS16949) ausgerichtet. Prozessorientiertes Denken und das Streben nach kontinuierlicher Verbesserung sind dabei prägend für die Unternehmenskultur geworden. "Unser Fokus liegt auf der Anlagenproduktivität, wir denken prozessorientiert und streben mit durchdachter Planung und konsequentem Controlling kontinuierlich nach Verbesserungen", erklärt der Fertigungsleiter, Ralf Diepers.
Verstecktes Potential
Als daher das Productcontrolling eindeutig ungenutztes Potential bei der Anlagenproduktivität nachweisen konnte, galt es, dieses möglichst schnell zu identifizieren und zu nutzen. Da das Unternehmen im Dreischichtbetrieb arbeitet, war schnell klar, dass nur eine automatisierte Datenermittlung und Auswertung zu einer weiteren Produktivitätssteigerung führen konnte. Zwar verfügten einzelne Anlagen im SMT-Bereich über Datenanalysefunktionen, die Auswirkungen von Störungen oder Optimierungen einzelner Anlagen auf die Gesamtverfügbarkeit der SMTLinie waren allerdings nicht immer nachvollziehbar und die gesteckten Produktivitätsziele ließen sich so nicht erreichen.
Auf der Suche
"Bei der Suche nach einer geeigneten Lösung stießen wir auf das Promatix-System Linealyzer. Dargestellt war die Auswertung einer SMT-Linie die quasi unserer Linienkonfiguration entsprach", erinnert sich Diepers. Zudem war das System für SMT-Linien ebenso wie für andere Anlagen ausgelegt. Helbako wollte drei SMT-Linien und zwei automatisierte Anlagen im Backendbereich analysieren und zwar mit einem einheitlichen System.
Der Linealyzer deckt von der Managementübersicht bis hin zur Detailanalyse einzelner Linienstörungen alle Anforderungen an ein Produktionsdatenerfassungssystem ab und ermöglicht auch die Anbindung an das SAP-System, um die Sollwerte für die Linienleistung zu übernehmen.
Auswertungen von Detaildaten wie Rüstzeiten, Störungsgründe und Ähnliches sind auf Knopfdruck verfügbar. Ausgestattet mit allen erforderlichen Funktionen für systematische Analysen und ein Shopfloormanagement bildet das System die Grundlage für schnelle zielgerichtete Analysen zur Produktionsoptimierung.
Lean-Management
Seit 2014 optimiert der Automobilzulieferer die Fertigung mit Lean-Ansätzen. Wesentliche Punkte sind die Verringerung von Durchlaufzeiten und die Erhöhungen von Anlagennutzungsgraden. Das Reportingsystem stellte dem Unternehmen im Lean-Projekt die wesentlichen Informationen zur Verfügung. Hierbei zeigte es sowohl technische Störungsgründe als auch organisatorische Themen durch gezielte Datenauswertung auf.
"Gerade in Bezug auf die Detailanalysen bei eventuell wieder auftretenden Abweichungen ist das System bei uns zu einem Standardwerkzeug für die Führungskräfte und Produktionsmitarbeiter geworden", berichtet Diepers.
"Mir war eswichtig, die Mitarbeiter nicht mit zusätzlicher Arbeit zu belasten.
Die Fehlerkommentierung sollte schnell gehen und einfach sein", übernimmt der für den SMT-Bereich Verantwortliche Andreas Schneider. Diese Anforderung erfüllt die Struktur der Bedienoberfläche.
Durch den Online-Monitor über den SMTLinien sind alle Mitarbeiter immer über den aktuellen Stand der Schicht informiert.
Das führte dazu, dass das Team aktiv an dem Projekt mitarbeitete und die Motivation für Verbesserungsvorschläge zugenommen hat.
System im Alltag
"Bei unserer Shopfloor-Managementrunde geht es überwiegend darum, wie sich die Linienausnutzungsgrade steigern lassen. Wir finden mit dem System auf einfache Weise Optimierungspotentiale und kontrollieren damit auch, ob die angesetzten Verbesserungen zum Erfolg führen" erklärt Schneider. Gerade aber auch kleinere Produktionsunterbrechungen, welche in der Vergangenheit nicht dokumentiert wurden, ließen sich mit Hilfe des Linealyzers ermitteln. So fiel zum Beispiel einmal auf, dass an einer der Linien sporadisch gegen Mitternacht eine durch die Reflow-Lötanlage verursachte Unterbrechung entstand. Die Produktionsunterbrechung dauerte bis zu fünf Minuten.
Als Ursache kommentierten die Kollegen der Nachtschicht eine nicht ausreichende Stickstoffversorgung. Ein umge-hend angesetztes ein Team zur Fehleranalyse konnte innerhalb weniger Tage die Ursache beheben. Mit dem Linealyzer ließ sich nachfolgend einfach dokumentieren, ob der Fehler wieder auftrat beziehungsweise, ob die durchgeführten Maßnahmen die gewünschte Wirkung zeigten.
Störgrößen aufdecken
An allen Arbeitsplätzen befindet sich ein Cockpit, das immer den Status der einzelnen Anlage aufzeigt. Dabei handelt es sich um die gleichen Informationen, die direkt an der Anlage den Mitarbeitern auf dem Online-Monitor zur Verfügung stehen. Damit unterstützt das System sowohl das Management als auch die Mitarbeiter in der Produktion. "Wir brauchen heute nicht mehr zu diskutieren, ob ein Problem tatsächlich existiert, das System teilt es uns als Tatsache mit", freut sich Schneider, "Wir verwenden unsere Energie darauf, die erforderlichen Dinge systematisch anzugehen und nachhaltig zu lösen." Das System hilft dabei, unbekannte Störgrößen aufzudecken und Verbesserungspotenziale zu ermitteln. Durch die Eliminierung der Stillstandzeiten, erreichte das Unternehmen bereits eine Steigerung der Liniennutzungsrade um 26 Prozent.
Seit der Schichtbericht auf dem Linealyzer läuft, arbeiten der ganze Bereich zudem papierlos. Die Informationen sind digital abgelegt, mit schneller Zugriffsmöglichkeit.
Für die Mitarbeiter bedeutet dies eine zeitliche Entlastung, da nur noch Kommentare für außergewöhnliche Ereignisse zu berichten sind. Dabei hat Promatix den Bericht exakt nach den Angaben des Automobilzulieferers umgesetzt.
Auch beim Umrüsten erweist sich das Reportingsystem als hilfreich. Bedingt durch die Auftragsstruktur sind bei Helkabo pro Schicht manchmal mehrere Rüstvorgänge erforderlich. Während des Rüstvorgangs zeigt der Online-Monitor die Linie in gelber Farbe an, so dass der Status "Rüsten" erkennbar ist. Ein Hauptansatz im Lean-Projekt war die drastisch Verkürzung dieser Rüstzeit. Linealyzer zeigt die Rüstzeit an und zeichnet sie automatisch auf, was die Ermittlung realer Rüstzeiten erlaubt. Außerdem lässt sich unmittelbar nachhalten, ob Bemühungen um eine Rüstoptimierung erfolgreich waren. Wiederholte Rüstzeitanalysen zwischen der theoretisch ermittelten und realen Rüstzeit sind problemlos durchführbar.
"Wenn etwas nicht wie geplant klappt und eine Kennzahl vom Plan abweicht, wollen wir wissen warum, dafür haben wir das System", erklärt Schneider. Um auch von unterwegs jederzeit den Überblick zu behalten, liefert ihm die Cockpitfunktion alle wesentlichen Informationen auf einem Bildschirm, den er über ein Smartphone einsehen kann.
Autor: Hubert Schönle
Geschäftsführer von Promatix
Promatix GmbH
Uhlmannstrasse 45
88471 Laupheim
Telefon: +49 (7392) 70916-38
http://www.promatix.de
Geschäftsführer
Telefon: +49 (7392) 709-1638
E-Mail: hubert.schoenle@promatix.de
Industrie 4.0
Dass sich diese Institutionen Gedanken um die Zukunft unseres Industriestandortes machen, ist sehr zu begrüßen, und die öffentliche Auseinandersetzung mit dem Thema Industrie 4.0 ebenso.
Was ist heute schon möglich?
Die Entwicklung der IK-Technologien hat mit immer kürzer werdenden Innovationszyklen rasant an Tempo zugenommen. Dabei wurde der Bedienkomfort der Systeme spürbar erhöht, so dass moderne Smartphones heute zum Standard von Jedermann gehören, privat und in der Freizeit.
Festzuhalten ist ebenso die Tatsache, dass in den meisten produzierenden Unternehmen die heute bereits verfügbaren Module aus dem Bereich Industrie 4.0 noch nicht oder nur teilweise eingesetzt werden. Da diese technischen Möglichkeiten nicht erst seit gestern existieren, sondern schon mehrere Jahre, scheinen die Gründe tiefer zu liegen und vielschichtiger zu sein.
Die technische Möglichkeit des Datentausches zwischen Produkt und Maschine und der Kommunikation von Maschine zu Maschine besteht schon seit vielen Jahren. Diese Möglichkeit wird auch partiell genutzt, an Stellen, wo es als „sinnvoll“ erachtet wird.
Da stellt sich nun die Frage nach dem Sinn?
Sinn in der Betriebswirtschaft machen nur solche Entscheidungen, die mittelbar oder unmittelbar einen Nutzen abbilden.
Im Produktionsumfeld heißt dies, die Investition bringt unmittelbar einen ROI innerhalb von 6 – 12 Monaten, oder einen Zugewinn in der Produktqualität oder in der Arbeitssicherheit.
Werden diese Bedingungen nicht erfüllt, erfolgt keine Investition!
Eine echte Hürde bei der Einführung von Industrie 4.0 Projekten wird also der Nachweis der Wirtschaftlichkeit sein. Selbst unter der Annahme, eine einheitliche Datenwelt sei durch die Entwicklung einheitlicher Schnittstellen wie Industrie 4.0 (im Werden) oder MTConnect gegeben, besteht immer noch die Problematik des existierenden und bewährten Anlagenparks, der noch nicht über neue Steuerungstechnik verfügt, dafür aber abgeschrieben ist, und ordentlich für Rendite sorgt.
Das Vorhandensein einheitlicher Datenschnittstellen und der erforderlichen Infrastruktur wird eine Einführung von Industrie 4.0 in den Fabriken sicher erleichtern, und auch auf der Kostenseite etwas für Entspannung sorgen. Ob damit auch die Motivation der Entscheidungsträger im Produktionsbereich steigt, bleibt abzuwarten.
Den Kollegen wurde in den vergangenen Jahren bei unzähligen „Lean Projekten“ vermittelt, die Dinge übersichtlich und einfach zu gestalten, KISS, und möglichst auf den Einsatz von IKT zu verzichten.
Im ganzheitlichen Einsatz von IKT auf der Shopfloor Ebene wird deshalb hier fälschlicherweise eher eine Gefahr als ein Nutzen gesehen, insbesondere, wenn es darum geht, funktionierende Produktionsanlagen in die Hände der „Informatik“ – hier der internen oder externen IT Abteilung zu legen!.
Nur kontinuierliche Überzeugungsarbeit kann hier Abhilfe schaffen.
Auch in der Kommunikation bezüglich des Themas Industrie 4.0 sollte stärker auf die Wirklichkeit eingegangen werden. Was in einem Labor wunderbar sich anwenden lässt, ist noch lange nicht für jeden Produktionsbetrieb sinnvoll, selbst bei extremen Wohlwollen.
Es gibt sicher viele Zwischenstufen, die heute schon einen ROI innerhalb 6 Monaten bringen, und die Rentabilität und die Wettbewerbsfähigkeit der Unternehmen stärkt.
Eine Herausforderung für die Einführung von Industrie 4.0 wird darin bestehen, den bereits existierenden Anlagenpark mit zu integrieren. Anlagen mit unterschiedlichem Baujahr und von verschiedenen Lieferanten gebaut, sollen steuerungstechnisch und datentechnisch so nachgerüstet werden, dass eine Produktion gemäß Industrie 4.0 möglich ist.
Ein solches Anliegen lässt sich allerdings wirtschaftlich nicht darstellen, und würde außerdem einen Anlagenausfall von mehreren Wochen nach sich ziehen.
Es bedarf also einer Lösung, die den erreichten Status an den Anlagen nicht gefährdet, sich wirtschaftlich darstellen lässt und schließlich die Vorteile aus Industrie 4.0 bietet, dies bei einem heterogenen Anlagenpark.
Moderne Produktionsmaschinen bieten heute schon eine unüberschaubare Menge an Daten, mit denen im Allgemeinen keiner etwas anzufangen weiß, mit Ausnahme dem Servicetechniker und der Programmierer des Herstellers.
Die Herausforderung heute besteht also darin, die Elemente aus Industrie 4.0 unmittelbar einzusetzen, die einen echten Kostenvorteil in Form von Produktivitätssteigerungen oder Flexibilitätssteigerung bringen.
Dieser Herausforderung entspricht zum Beispiel das Shop Floor Management System „Linealyzer“ von Promatix. Dieses System ist universell einsetzbar, da es keine Schnittstellen zu der Anlagensoftware benötigt, und ist schrittweise skalierbar bis zu einer Industrie 4.0 Funktionalität, immer mit dem Fokus auf den ROI der Kunden.
Dabei versteht sich das System als Unterstützung für den Mitarbeiter und das Management in der Produktion! Der Nutzen ist unmittelbar vorhanden, und für zukünftige Entwicklungen sind die Grundsteine gelegt.
Promatix GmbH
Uhlmannstrasse 45
88471 Laupheim
Telefon: +49 (7392) 70916-38
http://www.promatix.de
Geschäftsführer
Telefon: +49 (7392) 709-1638
E-Mail: hubert.schoenle@promatix.de
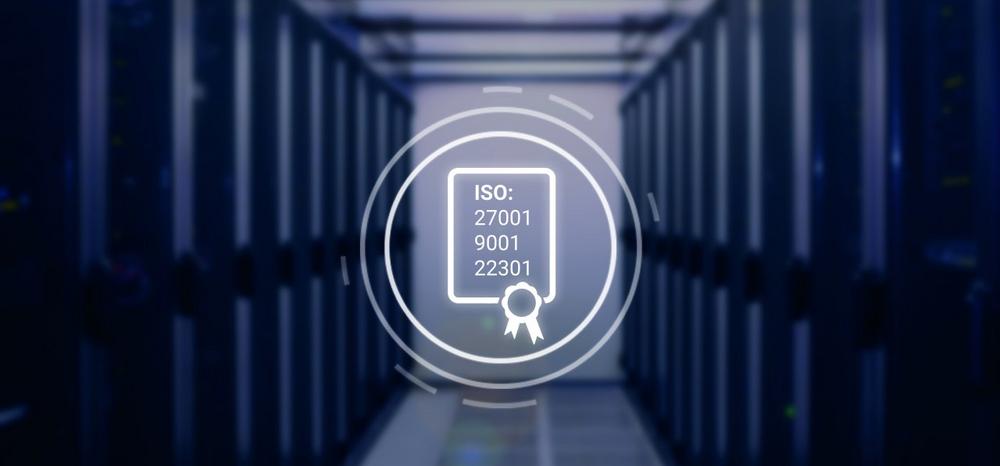
eurodata Rechenzentrum: ISO-Zertifizierung im Doppelpack
Business Continuity garantiert
Das ISO 22301-Zertifikat umfasst in erster Linie Aspekte des Business Continuity Managements. Es geht darum, Risiken zu minimieren und Vorsorgeprozesse zu definieren, damit im Notfall schnell und zuverlässig die erforderlichen Maßnahmen eingeleitet sowie die Datenverfügbarkeit garantiert werden können. „Damit wir unseren Kunden maximale Sicherheit bieten können, betreiben wir unsere Systeme in zwei infrastrukturell voneinander getrennten eigenen Rechenzentren. Zusätzlich werden die Daten in einem unabhängigen Rechenzentrum gespiegelt“, sagt Dieter Leinen, Vorstand der eurodata AG. Zudem werden das Rechenzentrum und die für den Betrieb erforderlichen Strukturen regelmäßig überprüft.
Aktualisierungs-Audit ISO 9001:2015
Über die ISO-Zertifizierung 9001 verfügt eurodata bereits. Jetzt wurden entsprechende Anpassungen vorgenommen, um auch der aktuellen Version ISO 9001:2015 gerecht zu werden. Dieser Standard sorgt für eine nachhaltige Qualitätssicherung sowie einen kontinuierlichen Verbesserungsprozess. Ziel von ISO 9001 sind die Minimierung von Risiken, Umsetzung von Compliance-Anforderungen sowie die Optimierung von Services. „Hinsichtlich dieser ISO-Norm sind wir schon länger optimal aufgestellt, sodass wir jetzt lediglich den ein oder anderen Dokumentationsaspekt ausbauen mussten“, ergänzt Dieter Leinen.
Darüber hinaus besitzt eurodata auch das ISO 27001-Zertifikat sowie die „Grüne Hausnummer“, die besagt, dass das Rechenzentrum besonders energieeffizient sowie klima- und ressourcenschützend arbeitet.
Weitere Informationen zum eurodata Rechenzentrum und seinen Qualitätsmerkmalen unter: https://www.eurodata.de/rechenzentrum
Die eurodata AG entwickelt und vermarktet cloudbasierte Softwarelösungen für Handelsnetze, Steuerberater und KMUs sowie Softwareprodukte zur Implementierung von Industrie 4.0 Lösungen. Mehr als 50.000 Kunden vertrauen den eurodata-Hochleistungsrechenzentren, einer sicheren Cloud "Made in Germany", mit professionellen Business Intelligence-, Web- und Cloud-Dienstleistungen. Damit übernehmen wir auch die Verantwortung für den reibungslosen Betrieb der Lösungen. Die eurodata AG wurde 1965 gegründet und hat ihren Hauptsitz in Saarbrücken. Heute fokussieren sich mehr als 500 Mitarbeiter nachhaltig auf den Erfolg unserer Kunden in ganz Europa. www.eurodata.de
eurodata AG
Großblittersdorfer Str. 257-259
66119 Saarbrücken
Telefon: +49 (681) 8808-0
Telefax: +49 (681) 8808-300
https://www.eurodata.de/
Leiter Corporate Marketing
Telefon: +49 (681) 8808-734
Fax: +49 (681) 8808-300
E-Mail: m.metz@eurodata.de
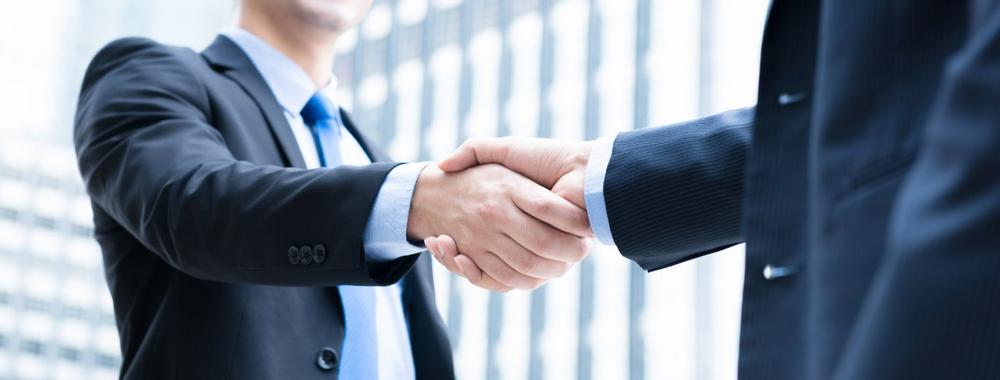
Gemeinsam zur Industrie 4.0
Ein gemeinsames Verständnis für fertigungsnahe IT-Systeme brachte MPDV auf der Suche nach einem Partner mit Arend Prozessautomation zusammen. Beide Kooperationspartner sind sich sicher, dass die Zusammenarbeit zu den gewünschten Win-Win-Effekten führen wird.
Dr.-Ing. Markus Jostock, Leiter Forschung & Entwicklung / Produktions-IT bei Arend Prozessautomation erläutert: „MPDV ist mit seinem MES-Produktportfolio ein idealer Partner für uns. Insbesondere der deutsche Mittelstand schätzt unsere ergebnisorientierte Herangehensweise und Flexibilität bei der Projektumsetzung. Durch die Kooperation mit MPDV werden wir noch stärker unserer Firmenphilosophie „Alles aus einer Hand“ gerecht.“
Die positiven Erwartungen wurden bereits in der Praxis bestätigt, nachdem gemeinsame Präsentationen bei interessierten Fertigungsunternehmen auf großes Interesse stießen und mittlerweile bereits erste konkrete Projekte in der Realisierungsphase sind. Auch beim gemeinsamen Workshop, der Ende 2017 vom Arbeitskreis Industrie 4.0 der IHK Trier durchgeführt wurde, überzeugten die Ideen, die den mehr als 30 anwesenden Fertigungsunternehmen für den Weg zur Smart Factory vorgestellt wurden.
Rainer Deisenroth, Vice President Sales & Marketing bei MPDV, ergänzt: „Auch wir freuen uns auf eine partnerschaftliche Zusammenarbeit mit Arend Prozessautomation. Die sich anbahnenden und bereits laufenden gemeinsamen Projekte stimmen uns dabei sehr zuversichtlich.“
Arend Prozessautomation GmbH (www.arend-automation.de) ist ein innovatives Unternehmen in Wittlich, dass sich den neuen und immer wieder wandelnden technologischen Herausforderungen der Industrie 4.0 stellt. Die Kernkompetenz des Unternehmens ist seit über 30 Jahren die Automation und wird zunehmend um die Technologieberatung und Serviceleistung im Bereich der Digitalisierung erweitert. Möglich wird dies durch das große Netzwerk in Form von Partnern und Mitgliedschaften, der Zusammenarbeit mit Hochschulen und Universitäten sowie durch die kompetenten Mitarbeiter des Unternehmens. Um den Kunden einen zusätzlichen Mehrwert bieten zu können, wurde im Jahr 2015 in eine betriebsinterne Entwicklungsabteilung investiert, die 2017 einen neuen IoT Datensammler mit innovativen Cybersicherheits-Merkmalen vorstellte. Durch die verknüpfte Einbindung in eine Vielzahl öffentlich-geförderter Forschungsprojekte (ZIM, BMWi) wächst die Kompetenz sowie die Kooperation zu weiteren starken Partnern.
MPDV Mikrolab GmbH (www.mpdv.com) mit Sitz in Mosbach entwickelt modulare Manufacturing Execution Systeme (MES) und greift dabei auf über 40 Jahre Projekterfahrung im Fertigungsumfeld zurück. MPDV bietet MES-Produkte, Dienstleistungen im MES-Umfeld sowie komplette MES-Lösungen an. Das Unternehmen beschäftigt aktuell 380 Mitarbeiter an insgesamt zehn Standorten in Deutschland, der Schweiz, Singapur, China und den USA. Anwender aus unterschiedlichen Branchen – von der Metallverarbeitung über die Kunststoffindustrie bis hin zur Medizintechnik – profitieren bereits von mehr als 1.000 Installationen der mehrfach ausgezeichneten MES-Lösungen von MPDV. Dazu zählen sowohl mittelständische Fertigungsunternehmen als auch international operierende Konzerne. Als TOP100-Unternehmen zählt MPDV zu den innovativsten Mittelständlern in Deutschland.
Manufacturing Execution Systeme (MES) unterstützen Fertigungsunternehmen dabei, ihre Produktionsprozesse effizienter zu machen, die Produktivität zu steigern und dadurch die eigene Wettbewerbsfähigkeit zu sichern bzw. auszubauen. Ein modernes MES versetzt Unternehmen in die Lage, fertigungsnahe Daten entlang der gesamten Wertschöpfungskette zu erfassen, auszuwerten und quasi in Echtzeit anzuzeigen. Die verantwortlichen Mitarbeiter können somit im Produktionsalltag kurzfristig auf ungeplante Ereignisse reagieren und geeignete Gegenmaßnahmen einleiten. Auf allen Ebenen unterstützt das MES sowohl kurzfristige als auch weitreichende Entscheidungen durch eine verlässliche Datenbasis.
MPDV Mikrolab GmbH
Römerring 1
74821 Mosbach
Telefon: +49 (6261) 9209-0
Telefax: +49 (6261) 18139
http://www.mpdv.com
Marketing Manager
Telefon: +49 (6202) 9335-0
E-Mail: n.neubig@mpdv.com
Marktstudie 2018: USU bei Kundenzufriedenheit auf Platz 1 und unter den Top-3-Marktführern
Für die Studie wurden 750 IT-Budgetverantwortliche in mittelständischen und großen Unternehmen in Deutschland per Telefon und online befragt. Mindestens 60% der Studienergebnisse basieren auf deren Bewertung. Die Analysten bestätigen: „Die USU ist problemlos in der Lage, sämtliche Kundenanforderungen im IT- und Enterprise-Service-Management-Markt zu erfüllen.“ Und sie fügen hinzu: „Der deutsche Mittelstand emanzipiert sich. Die Marktdominanz der ‚großen vier‘ Hersteller (BMC, CA, HP und IBM) ist (…) Historie. Deutsche Unternehmen und hier speziell der gehobene Mittelstand tendieren mehr und mehr zu lokalen, ebenfalls mittelständisch geprägten Unternehmen.“
Die befragten Personen bewerteten die Anbieter anhand spezifischer Kriterien in den Bereichen „Strategie“ und „Umsetzung“. Dazu zählen u. a. Faktoren wie Vision und Vermarktung, Firmenstabilität und Umsetzungskraft, Breite und Tiefe des Lösungsangebots, Markanteil und Wachstum, Kundenzufriedenheit und mehr. Bei der Kundenzufriedenheit erzielte die USU die beste aller Bewertungen.
Laut Research in Action ist das Wachstum im Bereich Enterprise Service Management (ESM) ungebrochen: Im Vergleich zu 2017 wächst der internationale Markt für ESM-Lösungen in 2018 um über 35 %. Weitere Wachstumsfelder in 2018 sind die Bereiche Automation (> 25 %), IT Financial Management (> 13 %) und Analytics (> 11 %). Die Studie unterstützt bei der Identifikation und Auswahl von Anbietern und informiert über aktuelle Markttrends zu IT-Investitionsvorhaben, zum Einsatz von Cloud-basierter Software, zur weiteren Entwicklung des De-facto-Standards ITIL® und mehr.
Die Marktstudie „Vendor Selection Matrix“ wurde von Research in Action im März 2018 veröffentlicht und steht kostenlos zum Download zur Verfügung auf valuemation.com/marktstudie-download
Die 1977 gegründete [url=https://www.usu.de/]USU AG[/url] gehört zu den größten europäischen Anbietern für IT- und Knowledge-Management-Software. Marktführer aus allen Teilen der internationalen Wirtschaft schaffen mit USU-Anwendungen Transparenz, sind agiler, sparen Kosten und senken ihre Risiken.
Der Geschäftsbereich [url=https://www.valuemation.com/de/?form_WMC=vm_hp_pp_pm]Valuemation[/url] unterstützt Unternehmen mit umfassenden, ITIL®-konformen Lösungen für das strategische und operative IT- und Enterprise Service Management. Kunden steuern damit sämtliche Serviceprozesse, schaffen Transparenz über ihre Servicekosten sowie ihre IT-Infrastruktur und können dadurch ihre Services effizient planen, überwachen und verrechnen.
Zum Einsatz kommt dabei die gleichnamige Software [url=https://www.valuemation.com/de/?form_WMC=vm_hp_pp_pm]Valuemation[/url], eine modulare, integrierte und ITIL®-zertifizierte Produktsuite. Sie wird im IT-Bereich großer und mittelständischer Unternehmen und bei IT Service Providern eingesetzt. Valuemation kommt aber auch in weiteren Servicebereichen wie z.B. Personal, Facility Management und Field Service Management zum Einsatz. Von Analystenhäusern und Zertifizierungsunternehmen wird Valuemation als weltweit führend eingestuft.
Die USU AG ist Teil der im Prime Standard der Deutschen Börse notierten USU Software AG (ISIN DE 000A0BVU28). Weitere Informationen: www.valuemation.com
USU Software AG
Spitalhof 1
71696 Möglingen
Telefon: +49 (7141) 4867-0
Telefax: +49 (7141) 4867-200
http://www.usu.com
Investor Relations
Telefon: +49 (7141) 4867-351
Fax: +49 (7141) 4867-108
E-Mail: f.sorge@usu-software.de
Corporate Communications
Telefon: +49 (7141) 4867-440
Fax: +49 (7141) 4867-909
E-Mail: t.gerick@usu-software.de
phronesis PR GmbH
Telefon: +49 (821) 444800
Fax: +49 (821) 4448022
E-Mail: moerz@phronesis.de
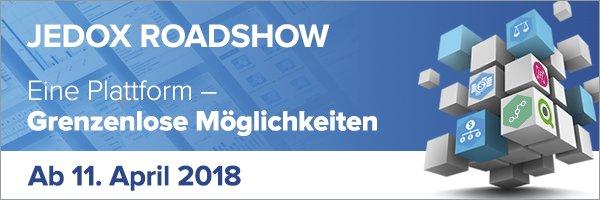
Moderne Planungslösungen für die digitale Transformation – Live auf der Jedox Roadshow 2018
Auch 2018 geht die Jedox AG auf Roadshow-Tour durch Deutschland, Österreich und die Schweiz: Fachanwender aus Controlling und anderen Abteilungen werden durch ein abwechslungsreiches Programm geführt und erhalten dabei praxisrelevante Informationen, wie sie die Jedox Software bei der digitalen Transformation unterstützt und Prozesse im Bereich Datenanalyse, Berichtswesen und Planung vereinfacht. Im Rahmen der halbtägigen Veranstaltungen erfahren Teilnehmer, wie operative und strategische Planung mit vordefinierten Jedox Modellen flexibel umgesetzt und individuell erweitert werden kann. Dabei stehen u.a. eine treiberbasierte Vertriebsplanung, integrierte Workflows, rollierende Forecasts und Szenario-Analysen im Vordergrund, die in Live-Präsentationen direkt umgesetzt werden.
Kundenerfolge und Jedox-Best Practices
Weiterer Programmpunkt ist die Präsentation konkreter Anwendungsszenarien durch namhafte Kunden, die aus erster Hand von ihren Erfahrungen im Einsatz der Jedox-Plattform berichten. Interessenten können in Kundenvorträgen – wie etwa des Logistikers IFCO Systems GmbH und der Immobiliengruppe wbg Nürnberg – mehr darüber erfahren, wie Unternehmen ihre Geschäftsprozesse mit Jedox maßgeblich optimieren konnten.
"Die digitale Transformation verändert Unternehmen und klammert dabei keine betriebliche Funktion aus. Ob Planung, operatives Geschäft, Vertrieb, Personal oder Finanzcontrolling – die Jedox Roadshow bietet Anwendern und Interessenten aller Abteilungen die Möglichkeit, die Vorteile einer effektiven Unternehmensplanung mit Jedox kennenzulernen und auszuschöpfen", sagt Niklas Panzer, Director Sales DACH der Jedox AG. "Wir freuen uns ganz besonders, die Highlights unserer neuesten Software-Version "Jedox 2018.1" vorzustellen", so Panzer weiter.
Die Roadshow beginnt am 11. April 2018 in Freiburg. Weitere Termine folgen in:
– Frankfurt (12. April 2018)
– Berlin (17. April 2018)
– Hamburg (18. April 2018)
– Düsseldorf (19. April 2018)
– München (24. April 2018)
– Wien (25. April 2018)
– Zürich (26. April 2018)
Mehr Informationen über die halbtägige Event-Reihe, das Programm, die Sprecher sowie die kostenfreie Anmeldung finden Sie unter: www.jedox.com/de/jedox-roadshow
Jedox vereinfacht Planung, Analyse und Reporting mit einer integrierten und Cloud-basierten Software-Suite. Anwender und Entscheider aus allen Fachabteilungen werden dabei unterstützt, datengetriebene Geschäftsprozesse selbstständig durchzuführen und Entscheidungen auf einer validen Datenbasis zu treffen. Über 2.300 Unternehmen in mehr als 140 Ländern nutzen Jedox bereits für ihre Realtime-Planungslösungen via Web, Mobile oder in der Cloud. Mit Standorten auf vier Kontinenten gehört die 2002 gegründete Jedox AG zu den führenden Anbietern von Business Intelligence- und Corporate Performance Management-Software. International verfügt das Unternehmen über ein Netzwerk aus über 200 zertifizierten Business-Partnern. Die unabhängigen Analysten Howard Dresner und BARC zeichnen Jedox regelmäßig für seine führenden Enterprise Planning-Lösungen aus. Vereinfachen Sie Ihre Planung mit Jedox und starten Sie noch heute Ihre kostenfreie Testversion auf www.jedox.com
Jedox AG
Bismarckallee 7a
79098 Freiburg im Breisgau
Telefon: +49 (761) 15147-0
Telefax: +49 (761) 15147-10
http://www.jedox.com
Head of Public Relations
Telefon: +49 (761) 151470
E-Mail: diana.kuch@jedox.com
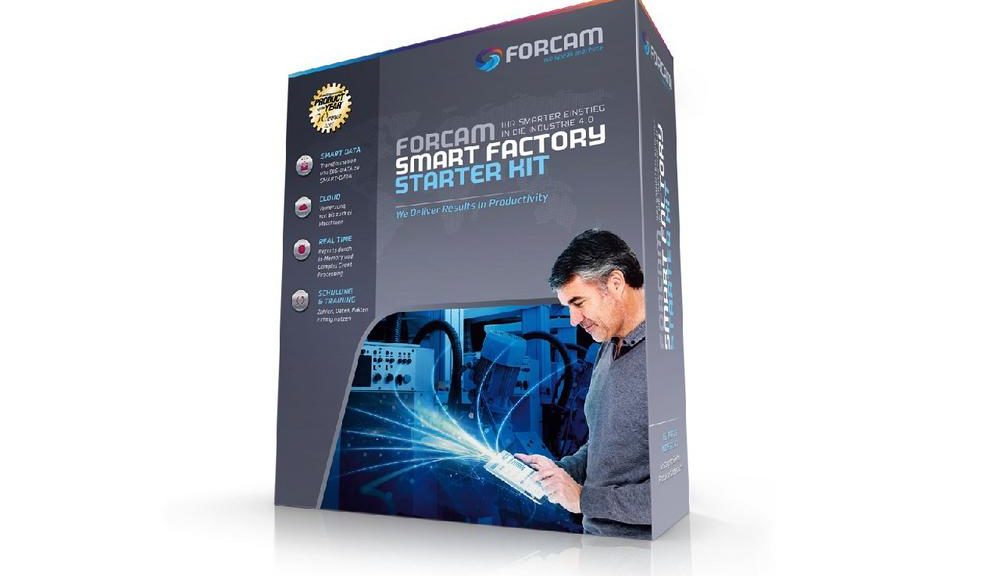
Die FORCAM GmbH wird von der Huber Verlag für Neue Medien GmbH mit dem INDUSTRIEPREIS 2018 geehrt
FORCAM FORCE™
Die FORCAM GmbH hat mit FORCAM FORCE™ eine ausgesprochen fortschrittliche Innovation entwickelt. FORCAM FORCE™ erfasst die Leistungsdaten von Maschinen und Anlagen. Diese werden ausgewertet und mit den Plandaten abgeglichen. Somit können schnell und einfach Produktivitäts-Potentiale ermittelt und umgesetzt werden. Die Daten sind für alle autorisierten Nutzer in Echtzeit verfügbar. Auch strategische Entscheidungen der Geschäftsführung können mit Hilfe der cleveren Lösung optimal getroffen werden.
Die FORCAM GmbH verspricht den Nutzern von FORCAM FORCE™ eine Produktivitätssteigerung um mindestens 10 Prozent. Maschinenarbeiter und Fertigungsleiter profitieren von der Innovation genauso wie Planer oder Manager. Die Lösung bietet übersichtliche Grafiken von der Feinplanung bis hin zum Fabrikvergleich.
„Die gesamte Industriebranche befindet sich im Wandel. Mit Industrie 4.0, dem Internet der Dinge und Smart Factory ist ein neues Zeitalter angebrochen. Mit ihrer produktivitätssteigernden Lösung FORCAM FORCE™ verhilft die FORCAM GmbH zahlreichen Unternehmen zu größerem Erfolg. Wir freuen uns, der FORCAM GmbH den INDUSTRIEPREIS 2018 in der Kategorie IT- und Softwarelösungen in der Industrie verleihen zu können“, so Rainer Kölmel, Geschäftsführer der Huber Verlag für neue Medien GmbH und Initiator des INDUSTRIEPREIS. Hier geht es zur Siegerliste.
FORCAM GmbH
Die FORCAM GmbH gehört zu den weltweit führenden Lösungsanbietern im Bereich Fertigungssteuerung und –Optimierung. Auf allen Kontinenten arbeiten mehr als 60.000 Maschinen mithilfe der Software von FOCRAM effizienter und kontrollierter. Damit sichert das Unternehmen die Wirtschaftlichkeit und den technischen Vorsprung zahlreicher bedeutender Industrieunternehmen.
Weitere Informationen zur IT-Lösung FORCAM FORCE™ finden Interessierte hier.
Mit Standort in Karlsruhe hat sich der Huber Verlag für Neue Medien innerhalb weniger Jahre als einer der größten Anbieter für Direkt-Informationsdienste etabliert. Die große Vielfalt der Verlagsprodukte und Medien deckt sämtliche Bereiche moderner Presse- und Öffentlichkeitsarbeit ab. Über die it-Medien liefert der Verlag seinen Lesern regelmäßig aktuelle Branchen-News. Die beliebte it-ZEITUNG, der Brennpunkt Mittelstand, der seminarSPIEGEL aktuell sowie der Newsletter Sales & Marketing erreichen zusammen über 140.000 Unternehmen und B2B-Entscheider.
Ergänzt wird das Angebot durch den MIT-Blog, das Online-Magazin life-on sowie verschiedene Social-Media-Kanäle.
Initiative Mittelstand (Huber Verlag für Neue Medien GmbH)
Lorenzstr. 29
76135 Karlsruhe
Telefon: +49 (721) 15118-0
Telefax: +49 (721) 15118-11
http://www.IMittelstand.de