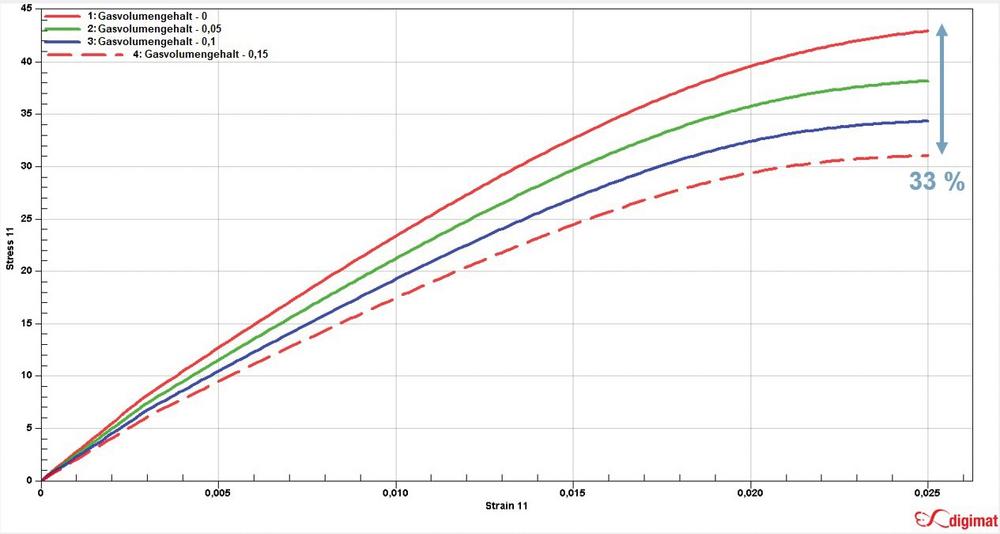
Ganzheitliche virtuelle Produktentwicklung
Treibende Kräfte und Weiterentwicklungspotential zeigen sich in den letzten Jahren verstärkt vor allem im Bereich Leichtbau. Dies nicht zuletzt, da sich hauptsächlich auch aus der Automobilindustrie Handlungszwänge hinsichtlich Reduktion der CO2 Emissionen ergeben. Neben Herstellungsverfahren der Faserverbundtechnologie geraten dabei zunehmend auch Prozesse und Verfahren der Spritzgussverarbeitung in den Fokus einer notwendigen Veränderung, eines erforderlichen progressiven Fortschritts. Einerseits steigt die Komplexität der Produkte, andererseits stehen Faktoren, wie die notwendige Reduktion der Produktionsschritte, anspruchsvolle Designanforderungen sowie auch höchste Erwartungen an die mechanischen Eigenschaften des finalen Produktes, als Schwerpunkte des Herstellungsprozesses im Raum.
Ein Verfahren, das aufgrund seines Potenzials immer mehr in den Fokus rückt, ist unter anderem das Schäumen von Kunststoffen, gemeint ist sowohl das chemische als auch das physikalische Schäumen. Notwendigerweise stehen bei Einführung dieser innovativen Technologie Investitionen an, neben den offensichtlich monetären, zusätzlich auch Investitionen in die Infrastruktur, die Produktentwicklung, die Ausbildung des Personals, die Aufrüstung der technischen Ausstattung und resultierende Umstrukturierungen der Arbeitsabläufe. So musste anfangs ein, ursprünglich für den Kompaktspritzguss ausgelegtes Werkzeug, rein verfahrenstechnisch angepasst werden. Die Anpassungen verliefen mit teils sehr unterschiedlichen Erfolgen, waren entsprechend breit gefächert und oft schwer kalkulierbar. Im positiven Fall konnten tatsächlich Gewichtsreduktionen erzielt werden. Aber es gab auch die negativen Fälle, bei denen die Resultate nicht den Erwartungen entsprachen. Das Für und Wieder zum Herstellungsverfahren „Schäumen“ gestaltet sich dementsprechend durchaus zwiespältig. Es ist nach wie vor eine Technologie mit Potential, aber auch eins, in das noch einiges an Entwicklungs- und Forschungsaufwand eingebracht werden muss.
Doch wie sieht es nun tatsächlich auf der Seite der Entwicklung geschäumter Bauteile aus? Bis heute werden Aufgaben und Schritte meist getrennt voneinander betrachtet, analysiert und angegangen. So erfolgt einerseits die Entwicklung des Produktes direkt vom Designer zum Werkzeugkonstrukteur. Zusätzlich führt ein Produktentwicklungsweg zu einer weiteren Abteilung, welche unabhängig von der Analyse und Betrachtung des Prozesses, Berechnungen im Rahmen der mechanischen Simulation durchführt. So erfolgt, die Simulation des Herstellungsprozesses in der Regel im Produktdesign und/oder in der Werkzeugkonstruktion. Dort gilt es die grundsätzliche Herausforderung zu meistern, erforderliche Anpassungen des Prozesses in den passenden, effektiven Arbeitsschritten und -abläufen zu realisieren, ganz selbstverständlich zu integrieren. Im Rahmen des Produktdesigns müssen beispielsweise Wandstärkenverhältnisse von Grundkörpern und Rippen überdacht werden. Auch in der Werkzeugkonstruktion werden Anpassungen notwendig, zum Beispiel hinsichtlich der Anbindungen.
Interessant für die Produktentwicklung ist aber auch, wie sich geschäumte Produkte unter mechanischer Last verhalten und wie deren Auslegung erfolgen sollte. Traditionell werden diese Betrachtungsschritte bisher in separaten Abteilungen vollzogen, eine Folge des unterschiedlichen Fokus des jeweiligen Aufgabenfeldes.
Seit einigen Jahren stehen hinsichtlich des Herstellungsverfahrens „Schäumen“ zunehmend auch Fragestellungen, wie die der Verarbeitung von faserverstärkten Kunststoffen im Fokus. Ein Verfahren mit enormen Entwicklungspotential vor allem in Blickrichtung „Leichtbau“. Die „üblichen“, bereits dargestellten, unabhängigen Produktentwicklungsschritte finden sich auch hier. Doch wird damit das Potential der Technologie vollständig und effektiv ausgenutzt? Ist ein Umdenken erforderlich, da zielführender? Und falls ja, welche technologischen und vor allem welche zeitlichen und finanziellen Auswirkungen haben diese Anpassungen?
Zur Beantwortung dieser Fragestellungen gilt es zunächst, den aktuellen Status zu bilanzieren. So stellt man fest, dass die zu einer Verbesserung notwendigen Werkzeuge häufig bereits existieren. Ebenfalls stellt sich nicht die Frage, wie mit diesen Werkzeugen umgegangen wird. Sondern vielmehr, wie gewonnene Resultate bewertet, eingesetzt und wie sie bzw. an wen sie kommuniziert werden.
Ein elementarer Aspekt liegt in der üblichen Herangehensweise bei der mechanischen Auslegung von Produkten, egal ob aus faserverstärkten Kunststoffen, mittels physikalischen oder chemischen Schäumens oder ähnlichen Verfahren hergestellt. Denn diese Betrachtungsmethode erfolgt meist unter der Annahme der gleichen mechanischen Eigenschaften für das gesamte Bauteil. Doch genau hier, liegt der Knackpunkt, durch diese Vorgehensweise werden die Möglichkeiten dieser Technologien deutlich reduziert und unvollständig ausgeschöpft, da nur einseitig betrachtet.
Welches Potential liegt in der Verknüpfung dieser Arbeitsschritte – die der Betrachtung des Prozesses und die der mechanischen Eigenschaften – zu einem Kreislauf verborgen?!! – In der Vereinigung zweier bisher unabhängiger Komponenten in einem Kreislauf, um die Substanz der virtuellen Produktentwicklung maßgeblich zu ergänzen, exponentiell zu verbessern.
So trivial es auch heute noch klingen mag, eine gute Basis aller Schritte liegt in der Durchgängigkeit der Konstruktionsdaten. Der Einsatz verschiedener CAD-Programme ist bis heute eine Quelle möglicher resultierender Herausforderungen. So sind die Details jedes CAD-Kernels (nicht CAD-Programmes) nicht einheitlich und es kann durch Datenimport und -export zu unerwünschten Überlappungen von Flächen oder anderen Fehlern kommen. Da zur Erzeugung von Produktdesign und Werkzeugkonstruktion oft zweierlei CAD-Programme eingesetzt werden, tritt dieses Phänomen meist häufig auf. Zur notwendigen Nacharbeit bzw. Aufbereitung der Daten für die Simulation stehen sowohl CAD-Programme als auch darauf spezialisierte Softwaretools zur Verfügung.
Die Prozesssimulation liefert die Basis für die Bewältigung möglicher, zu erwartender, zu bewältigender Herausforderungen aufgrund des Herstellungsprozess, des Produktdesign, der Werkzeugkonstruktion und/oder des Werkstoffs geschäumter Bauteile. Berechnet, analysiert, bewertet und optimiert wird der gesamte Prozess von Füllung über Abkühlung bis hin zur Simulation der Deformation. Zu den geläufigen Simulationsergebnissen des Schäumens zählen vor allem zwei, welche die einen teils erheblichen Einfluss auf weiteren Entwicklungsschritte haben. Zum einen die Zellgrößen- und zum anderen die Zelldichteverteilung. Diese beiden Resultate erlauben nicht nur einen Rückschluss bezüglich „kosmetischer“ Fragenstellungen. Vielmehr widerspiegeln sie, wie stark die lokale Randschicht ausgeprägt, ob mit mehr oder weniger Schlieren auf der Oberfläche zu rechnen und wie hoch die zu erwartende Deformation des finalen Bauteils ist. Weiterhin klären sie auch verfahrensrelevante Fragestellungen, ob möglicherweise der Einsatz einer variothermen Temperierung empfehlenswert ist.
Der entscheidende Aspekt für die erfolgreiche Kopplung zweier bisher unabhängiger Komponenten – der Prozesssimulation und der Strukturmechanik – in einem Produktentwicklungskreislauf liegt nun im folgenden Schritt. Lange Zeit wurden, wie bereits dargelegt, diese beiden Methoden zur Herstellung sicherheitsrelevanter Produkte außen vorgelassen, da eine durchgängige simulative Prozess- wie auch mechanische Simulation nicht möglich sein sollte. Doch bei Berücksichtigung einiger wichtiger Aspekte gelingt genau das und darüber hinaus ergibt sich sogar ein maximal nutzbarer positiver Effekt. Die Beschreibung der entstandenen Zellen kann über Porositätsergebnisse von Moldex3D (für die Prozesssimulation eingesetztes Simulationsprogramm) an das Softwaretool Digimat zwecks Materialmodellierung übergeben werden. Die daraus resultierenden lokal unterschiedlichen Materialkennwerte werden dann an die strukturmechanische Simulation weitergegeben. Die Relevanz dieser Vorgehensweise wird in der Abbildung 1 verdeutlicht. Hier ist ein Spannungs-Dehnungsdiagramm in Abhängigkeit von der Mikrostruktur abgebildet.
Auf diesem Weg wird sichergestellt, dass die lokalen unterschiedlichen Zustände des Materials entsprechend berücksichtigt werden und somit anschließend gezielte Korrekturen des Bauteils in Bezug auf die mechanischen Eigenschaften realisiert werden können. Die anschließende Überprüfung der geometrischen Anpassungen erfolgt wieder mittels Prozesssimulation. Resultierende, optimierte Prozesssimulationsergebnisse werden wiederholt zum Export in die Mechanik vorbereitet. Der Kreislauf schließt sich. Dieser Vorgang kann manuell durchgeführt werden. Allerdings bietet sich hier auch die Möglichkeit eines weitestgehend automatischen Optimierungsablaufes. Ein Vorteil der Optimierung liegt darin, dass neben dem klassischen DoE-Ansatz auch geometrische Anpassungen ermöglicht werden, bis hin zur automatischen Topologieoptimierung.
Letztendlich stellt sich die Frage, wie sehr lohnt sich dieser Aufwand? Anhand eines konkreten Bauteils, einer Blende (siehe Abbildung 2) sollen die Vorteile näher dargestellt werden.
Im Rahmen der Prozesssimulation wurde neben dem Bauteil zusätzlich das gesamte Temperier- und Verteilersystem dargestellt, berechnet und analysiert, hier in Abbildung 3 ersichtlich.
In Abbildung 4 wird die simulierte Zellstruktur (links) mit einer CT Aufnahme verglichen. Ersichtlich ist eine komplette Übereinstimmung der berechneten Werte und der Realität. Die relevanten Resultate der Porosität aus dem Schäumprozess wurden anschließend an Digimat übertragen. Mit den dort erzeugten Materialkarten wurde anschließend innerhalb der FEA ein Drei-Punkt-Biegeversuch berechnet. Parallel dazu wurde dieser Versuch ebenfalls mit dem realen Bauteil durchgeführt.
Das resultierende Kraft/Weg Diagramm ist in der Abbildung 5 abgebildet. Es ist hier deutlich zu erkennen, wie sehr die isotropen Ansätze von der realen Messung (hier in pink) abweichen. Dies gilt mitunter nicht nur für den quantitativen Verlauf, sondern auch vor allem dem qualitativen Aspekt des Versagens. In diesem Diagramm sind ferner die ersten Resultate (in blau) der durchgängigen Berechnung dargestellt, welche sowohl im qualitativen wie auch quantitativen eine sehr gute Übereinstimmung zur Realität darstellt.
Zusätzlich wurden mit dem gleichen Produkt (der Blende) auch Optimierungsläufe durchgeführt. Der Vergleich begann mit der Betrachtung des Verfahrens des Kompaktspritzguss gegenüber dem des Schäumens. Damit konnte das Bauteilgewicht bereits um 10.1% reduziert werden. In einem weiteren Schritt wurde das Produktdesign optimiert. So wurde die Rippenstruktur auf der Unterseite der Blende mittels des sogenannten Sizeing‘ optimal an die geforderten Randbedingungen angepasst. Ein Anpassungsschritt gemäß der Optimierung aufgrund mechanischer Eigenschaften. Erzielt wurde eine weitere Reduktion des Gewichtes um 5%. Zudem wurde die Optimierung des Fertigungsprozesses in den Produktentwicklungsprozess eingebunden. So konnte letztlich dank der ganzheitlichen Betrachtungsweise und des fortschrittlichen Optimierungsansatzes eine Gewichtsreduktion von 25% bei gleichzeitiger Verringerung der fertigungsrelevanten Deformationen von gut 50% und einer Verkürzung der Zykluszeit bei der Herstellung von 10% erzielt werden.
Die ganzheitliche virtuelle Entwicklung eines Produktes (siehe Abbildung 6) verdeutlicht zwei wesentliche Aspekte – zum einen ist mit Zuhilfenahme der dargestellten Methodik eine ganzheitliche simulative Betrachtung geschäumter Bauteile real und erfolgreich möglich. Und zum zweiten wird es ganz offensichtlich, auch in Hinblick des Bereiches Leichtbau, in dieser Herangehensweise verbirgt sich ein Potential, das nur darauf wartet, ausgereizt zu werden!
Danksagung:
Wir bedanken uns bei:
- dem Institut für Werkstofftechnik der Universität Kassel für die Unterstützung im Rahmen der Materialcharakterisierung und Durchführung der praktischen mechanischen Versuche,
- der Ineos Styrolution Europe GmbH für das bereitgestellt Material,
- der Firma F. & G. Hachtel GmbH & Co. KG für die Unterstützung bei den CT Aufnahmen sowie
- der Firma Volume Graphics für die Analyse der CT Aufnahmen.
Das resultierende Kraft/Weg Diagramm ist in der Abbildung 5 abgebildet. Es ist hier deutlich zu erkennen, wie sehr die isotropen Ansätze von der realen Messung (hier in pink) abweichen. Dies gilt mitunter nicht nur für den quantitativen Verlauf, sondern auch vor allem dem qualitativen Aspekt des Versagens. In diesem Diagramm sind ferner die ersten Resultate (in blau) der durchgängigen Berechnung dargestellt, welche sowohl im qualitativen wie auch quantitativen eine sehr gute Übereinstimmung zur Realität darstellt.
Zusätzlich wurden mit dem gleichen Produkt (der Blende) auch Optimierungsläufe durchgeführt. Der Vergleich begann mit der Betrachtung des Verfahrens des Kompaktspritzguss gegenüber dem des Schäumens. Damit konnte das Bauteilgewicht bereits um 10.1% reduziert werden. In einem weiteren Schritt wurde das Produktdesign optimiert. So wurde die Rippenstruktur auf der Unterseite der Blende mittels des sogenannten Sizeing‘ optimal an die geforderten Randbedingungen angepasst. Ein Anpassungsschritt gemäß der Optimierung aufgrund mechanischer Eigenschaften. Erzielt wurde eine weitere Reduktion des Gewichtes um 5%. Zudem wurde die Optimierung des Fertigungsprozesses in den Produktentwicklungsprozess eingebunden. So konnte letztlich dank der ganzheitlichen Betrachtungsweise und des fortschrittlichen Optimierungsansatzes eine Gewichtsreduktion von 25% bei gleichzeitiger Verringerung der fertigungsrelevanten Deformationen von gut 50% und einer Verkürzung der Zykluszeit bei der Herstellung von 10% erzielt werden.
Die ganzheitliche virtuelle Entwicklung eines Produktes (siehe Abbildung 6) verdeutlicht zwei wesentliche Aspekte – zum einen ist mit Zuhilfenahme der dargestellten Methodik eine ganzheitliche simulative Betrachtung geschäumter Bauteile real und erfolgreich möglich. Und zum zweiten wird es ganz offensichtlich, auch in Hinblick des Bereiches Leichtbau, in dieser Herangehensweise verbirgt sich ein Potential, das nur darauf wartet, ausgereizt zu werden!
Danksagung:
Wir bedanken uns bei:
dem Institut für Werkstofftechnik der Universität Kassel für die Unterstützung im Rahmen der Materialcharakterisierung und Durchführung der praktischen mechanischen Versuche,
der Ineos Styrolution Europe GmbH für das bereitgestellt Material,
der Firma F. & G. Hachtel GmbH & Co. KG für die Unterstützung bei den CT Aufnahmen sowie
der Firma Volume Graphics für die Analyse der CT Aufnahmen.
SimpaTec Simulation & Technology Consulting GmbH
Wurmbenden 15
52070 Aachen
Telefon: +49 (241) 565276-0
Telefax: +49 (241) 565276-99
http://www.simpatec.com
Manager PR & Social Media
Telefon: +49 (241) 565276-0
Fax: +49 (241) 565282-89
E-Mail: n.baxter@simpatec.com
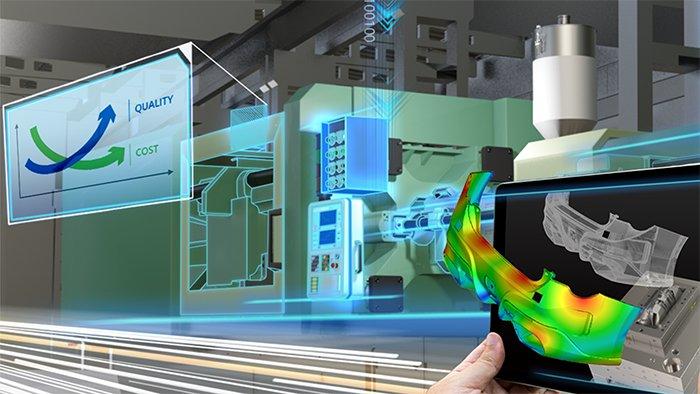
Vorreiter in der intelligenten Fertigung – Moldex3D 2021
Exaktere und maßgeschneiderte Simulationsberichte
In Moldex3D 2021 ist es vollends gelungen, sowohl die Vorhersagegenauigkeit als auch maßgeschneiderte Lösungen raffiniert zu verbessern. So kombiniert Moldex3D 2021 jetzt für die häufig zum Einsatz kommende Schwindungs- und Verzugsvorhersage beim Spritzgießen die Material- und Spannungseigenschaften des Kunststoffs beim Phasenwechsels in der Nachdruckphase. Die Folge – eine noch exaktere und präzisere Vorhersagegenauigkeit wird möglich. Zusätzlich stehen Anwendern genauere Ergebnisse bei der Verzugsvorhersage von fasergefüllten Materialien zur Verfügung. Denn die Implementierung der Simulation mechanischer Eigenschaften resultiert in einer erheblichen Steigerung der Berechnungsgenauigkeit von Kurzfasermaterialien. Eine deutliche Verbesserung der Funktionen für Kurvendesign und -bearbeitung, erlauben nun die effiziente und erfolgssichere Erzeugung qualitativ noch hochwertigere Netze. Mit einem neuen Assistenten für Maschinendüsen sowie verbesserten Assistenten für Anguss, Angusskanäle und Kühlkanäle können Anwender Konstruktionen nun mit Hilfe von Parametern und automatischer Netzgenerierung ideal optimieren, so dass Designvalidierungen noch einfacher und exakter werden. Je nach Werkzeugbeschaffenheit werden im Berufsalltag unterschiedliche Analyseberichte benötigt. Mit Moldex3D Studio 2021 können Berichtsformate individuell angepasst und exakt ausgewählt werden, welche Elemente final angezeigt werden sollen.
Präzision für modernste Verfahren und Verbundwerkstoffen
Der intensive Entwicklungsaufwand, der in neue Features, Funktionalitäten und Optimierungen im Bereich der „Non-Matching-Technologie“ investiert wurde, hat sich definitiv ausgezahlt. So wurde in der neuesten Version Moldex3D 2021 z.B. auch eineMethodik für die Konstruktion von mehrlagigen Fasermatten (DU-Profil/Gewebe) implementiert. Diese neue Funktion verkürzt die Vernetzungszeit enorm und verbessert zusätzlich die Genauigkeit der RTM-Simulation (Resin Transfer Molding) um ein Vielfaches.
Im Bereich der Simulation von Schäumverfahren sind ebenfalls Neuerungen und Weiterentwicklungen zu vermelden – erweiterte physikalische Abbildungsmöglichkeiten dank eines neu integrierten mikroskopischen Schäumungsvorhersagemodells erhöhen deutlich die Vorhersagegenauigkeit der bestehenden Module für die verschiedenen Prozesse des Schäumens.
Zusätzlich unterstützt das neue Release Moldex3D 2021 die Simulation von thermoplastischen Endlosfaserplatten aus Fiber-mat. Durch die Einstellung der Materialeigenschaften von Endlosfasern können Anwender nun analysieren, wie sich die Faserorientierung auf die Produktqualität und die mechanische Festigkeit auswirkt – ein direkter positiver Einfluss auf eine noch effizientere und exaktere Produktentwicklung.
Schnelle, detaillierte und multifunktionale IC-Packaging-Prozess-Simulation
Der Trend zur Intellektualisierung und der Wunsch nach Elektrofahrzeugen erzeugt einen steigenden Bedarf an zuverlässigen, leistungsfähigen IC-Produktleistung in der globalen Industrie. Eine fortschrittliche IC-Packaging-Technologie ist dabei unerlässlich und spielt eine zunehmend wichtigere Rolle im Herstellungsprozess. Die Integration neuer „Potting-Simulationsfunktionen“ stehen dafür dem IC-Packaging-Anwender unterstützend zur Verfügung. Zudem können mit Hilfe des „Pre-Processing Wizard“ schnell und zuverlässig qualitativ hochwertige Netze generiert werden. Das spart Zeit bei der Modellvorbereitung, ermöglicht effiziente, optimale Validierungen des IC-Packaging-Designs und resultiert letztlich in einer erheblichen Reduzierung der Kosten für aufwendige „Trial & Error“ Durchläufe.
Zusätzliche CAD-Werkzeuge und verbesserter Solver
Moldex3D 2021 bietet dem Anwender zudem zahlreiche weitere Verbesserungen, die die täglichen Arbeitsabläufe enorm erleichtern. Zu den Highlights gehören ebenfalls neuen Funktionen für das Erzeugen und Modifizieren von CAD-Daten. So befähigt eine noch effizientere und flexiblere Modellvorbereitung in Moldex3D Studio den Anwender zu Reparaturen und Modifikationen, ohne dass eine zusätzliche CAD-Software eingesetzt werden muss. Variantenvergleiche verschiedener Bauteil- oder Angusskonstruktionen sind in Moldex3D damit im Handumdrehen erstellt.
Ein weiteres interessantes optionales Feature um noch realistischere Ergebnisse vorhersagen zu können, ist die neue Berechnungsmethode für die Schwindungsberechnung. Verbesserungen in Zusatzmodulen, z.B. DOE und Extrusion, liefern in Bezug auf die Modellierung und Auswertung darüber hinaus zusätzliche analytische und simulationstechnische Erkenntnisse.
SimpaTec bietet seit 2004 professionelle Ingenieurleistungen und unterstützt die Entwicklung und Optimierung von Spritzgussteilen in jeder Phase des Prozesses. Der diesjährige MiDay Germany 2021, der am 14. September 2021 in Böblingen stattfindet, ist eine ideale Gelegenheit, sich über die neuesten Entwicklungen zu informieren. Überzeugen Sie sich selbst wie die SimpaTec, durch Kombination qualitativ hochwertiger Simulation und kundennaher Beratungsdienstleistung, ein kompetenter Partner für die kunststoffverarbeitende Industrie sein kann und den Weg zur Produkt- und Prozessoptimierung möglichst kurz und effizient gestaltet.
SimpaTec Simulation & Technology Consulting GmbH
Wurmbenden 15
52070 Aachen
Telefon: +49 (241) 565276-0
Telefax: +49 (241) 565276-99
http://www.simpatec.com
Manager PR & Social Media
Telefon: +49 (241) 565276-0
Fax: +49 (241) 565282-89
E-Mail: n.baxter@simpatec.com
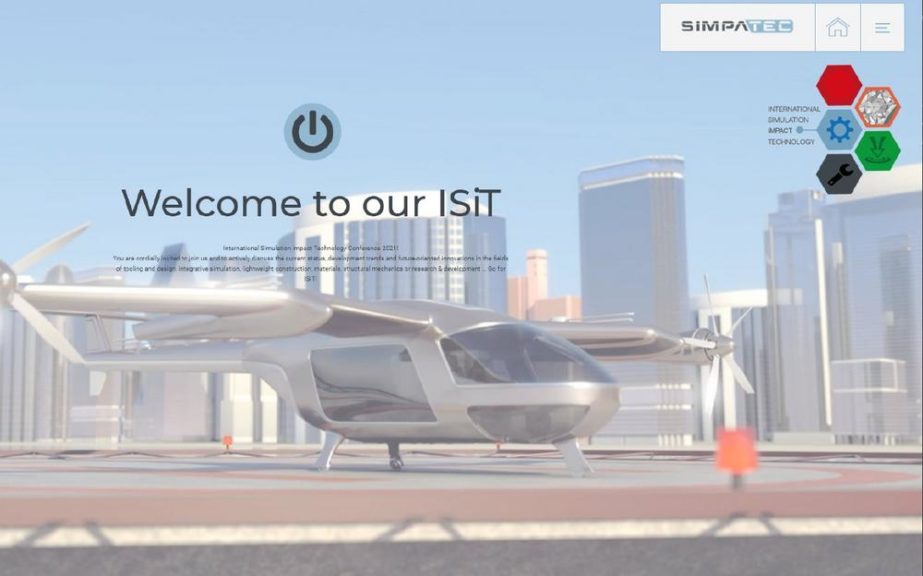
ISiT 2021 – ein voller Erfolg!
36 renommierte Fachexperten aus der ganzen Welt referierten über innovative Methoden, Technologien sowie Lösungskonzepte zur ganzheitlichen Entwicklung und Optimierung von Bauteilen, Werkzeugen und Prozessen im Spritzguss & FEM-Bereich. Im Mittelpunkt standen unter anderem auch neue Details über die ganzheitliche virtuelle Produktentwicklung, bei der mittels Kopplung der mechanischen und prozesstechnischen Entwicklung eines Bauteils – das Fundament für den späteren Erfolg des Bauteils oder eines effizienten Herstellungsverfahrens gelegt werden kann!
Ein weiterer Schwerpunkt der ISiT 2021 lag auf dem Thema KOMMUNIKATION!! – der Kommunikation zu und gemeinsam mit Referenten, Partnern, Fachexperten und vor allem auch Teilnehmern. Eine besondere Gelegenheit des direkten Wissenstransfers und Informationsaustausches schuf SimpaTec mit der Gestaltung virtueller Meetingräume – ideale Plätze für Networking, Diskussionen und die Beantwortung individueller fachspezifischer Fragen an SimpaTec’s Expertenteam, Referenten, ausgewählte Geschäftspartner oder natürlich auch im Kreise des anwesenden internationalen Fachauditoriums. Zusätzliches Informationsmaterial präsentierten ausgewählte Unternehmen im sogenannten Showroom, dort erhielten die Besucher eine weitere Möglichkeit, sich über die neuesten Produkte und Entwicklungstrends der Branche zu informieren.
SimpaTec bedankt sich herzlich bei allen Referenten, Geschäftspartnern und Sponsoren der ISiT für das außergewöhnliche persönliche Engagement und die tatkräftige Unterstützung bei der Realisierung des Veranstaltungskonzeptes – Go for ISiT! Aktuell hat der ‚ISiT Flieger‘ den Kurs gewechselt auf der Suche nach neuen faszinierenden und spannenden Fachthemen. SimpaTec erwartet seine Rückkehr mit etwas Ungeduld, um endlich das Gepäck sichten zu können und freut sich bereits jetzt auf einen weiteren gemeinsamen Rundflug mit ‚Punktlandung‘ in 2022!
SimpaTec GmbH – Break your limits. Challenge us.
Die Kernphilosophie der SimpaTec GmbH ist unser Antrieb und zur gleichen Zeit auch als Appell an unsere Kunden gerichtet:
"Break your limits"! Es ist eine Aufforderung an Jeden von uns, Barrieren zu überwinden, über seine Grenzen hinaus zu denken, sich so neue Horizonte zu erobern, mögen sie auch noch so kühn erscheinen.
Definieren und verfolgen Sie Ihre neuen Ziele und Projekte mit SimpaTec!
Mit Kompetenz, Erfahrung, Ehrgeiz und dem Einsatz modernster Softwaretechnologien setzen wir gemeinsam mit Ihnen neue Standards bei der ganzheitlichen Entwicklung und Optimierung von Prozessen, Bauteilen und Werkzeugen. Wir begegnen jeder noch so komplexen Fragestellung mit wissenschaftlicher Expertise. Aufgrund unserer Marktstellung und internationalen Präsenz, sind wir immer über die neuesten Forschungsergebnisse und Entwicklungstrends informiert.
SimpaTec ist damit Ihr erster Ansprechpartner und mit Sicherheit der führende Berater, um leistungsfähige und hochwirksame Software- und Dienstleistungspakete zu bündeln. Von der Konstruktion mittels CAD über die Prozessoptimierung bis hin zur Lastfallanalyse mit impliziten oder expliziten CAE-Anwendungen in allen Fragen stehen unseren Kunden hervorragend ausgebildete Mitarbeiter an acht verschiedenen Standorten – in Aachen, Hamburg, Reutlingen, Weimar (Deutschland), Schlierbach (Österreich), Guebwiller (Frankreich), Bangkok (Thailand) sowie in Charlotte, NC (USA) als kompetente Ansprechpartner zur Verfügung.
SimpaTec Simulation & Technology Consulting GmbH
Wurmbenden 15
52070 Aachen
Telefon: +49 (241) 565276-0
Telefax: +49 (241) 565276-99
http://www.simpatec.com
E-Mail: s.paul@simpatec.com
Manager PR & Social Media
Telefon: +49 (241) 565276-0
Fax: +49 (241) 565282-89
E-Mail: n.baxter@simpatec.com
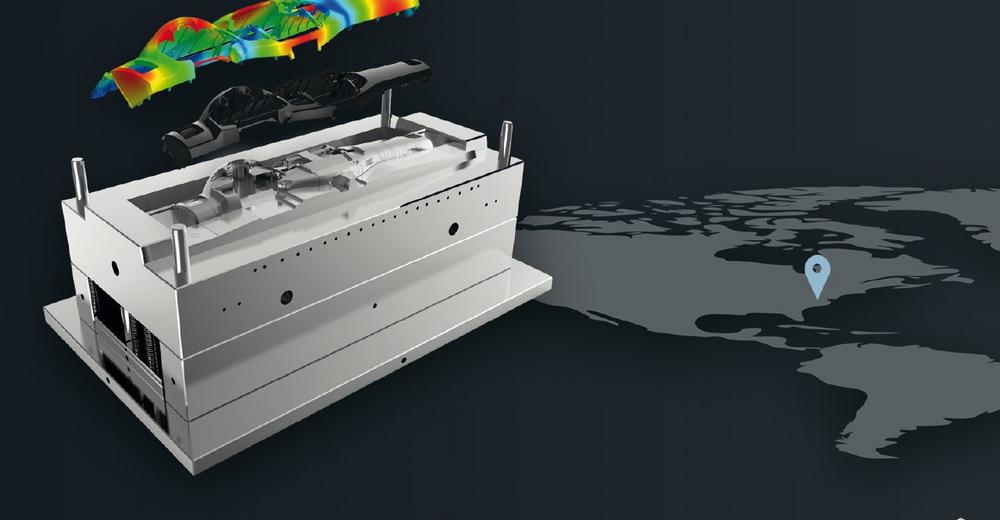
„SimpaTec überquert den großen Teich“
Die neue Location in Charlotte, North Carolina, bietet optimale, strategische Möglichkeiten, die Unternehmensaktivitäten maßgeblich zu intensivieren und zu qualifizieren. Die wichtigsten marktrelevanten Einflußfaktoren befinden sich außerdem im direkten Umfeld. „Wir sehen hier den optimalen Standort und die idealen Bedingungen, um neue Geschäftsbeziehungen aufzubauen, zu etablieren, stetig zu erweitern und unsere angestrebten Zukunftspläne im amerikanischen, kanadischen und mexikanischen Markt zu realisieren“, erklärt Cristoph Hinse, CEO von SimpaTec Inc.
Die kürzlich geschlossene Partnerschaft mit CONTURA® MTC, einem führenden Unternehmen in der Entwicklung konturfolgender Temperierungskonzepte, verstärkt zusätzlich SimpaTec’s Position als idealen Partner für alle Ingenieurdienstleistungen bezüglich der optimalen Werkezugtemperierung von Werkzeugeinsätzen kleiner oder großer Bauteile. Erzielt werden damit erhebliche kürzere Zykluszeiten, Verbesserungen der Bauteilqualität und Oberflächenbeschaffenheit sowie wesentlich reduzierte Produktionskosten. Herr Reiner Westhoff, Geschäftsführer von CONTURA® MTC, betont: „Wir sind sehr froh, einen so erfahrenen, kompetenten und fachkundigen Partner vor Ort in den USA zu haben, der sich intensiv um die Bedürfnisse aller bestehenden und zukünftigen Kunden kümmern kann. Wir freuen uns auf eine erfolgreiche Zusammenarbeit“.
Von dieser territorialen Erweiterung der Geschäftsaktivitäten werden aktuelle und potenzielle Kunden sowie Geschäftspartner immens profitieren. Wieso? SimpaTec ist jetzt auf drei Kontinenten (Amerika, Europa und Asien) vertreten, das Unternehmen rückt somit nicht nur räumlich in die Nähe seiner Kunden, sondern auch die unterschiedlichen Zeitzonen können so mühelos gemeistert werden. Das spart nicht nur Zeit, sondern garantiert zudem eine schnelle und effiziente Unterstützung. SimpaTec’s Fachexperten stehen sozusagen „rund-um-die-Uhr“ als Ansprechpartner für technischen Support, Dienstleistungen, Materialanfragen, beratende Gespräche oder auch Schulungen, etc. zur Verfügung – und das auch noch in der regional gängigen Landessprache. Ein weiterer Vorteil dieser globalen Präsenz ist die Wahrnehmung, Berücksichtigung und Integration lokaler marktspezifischer Anforderungen zum Wohle des Kunden.
SimpaTec freut sich schon sehr, die sich stellenden Herausforderung anzugehen, neue Horizonte zu erobern und frische, spannende, bisher unbekannte Aufgaben diesseits des Ozeans zu meistern. Überzeugen Sie sich selbst, wie das Unternehmen mittels effektiver Kombination hochwertiger Simulation und kundenorientierter Beratung zu Ihrem kompetenten Partner für die kunststoffverarbeitende Industrie avanciert. Gestalten Sie mit SimpaTec den Weg zur optimalen Produkt-, Werkzeug- und Prozessentwicklung so kurz und effizient wie möglich! Break your limits!
Break your limits. Challenge us.
Die Kernphilosophie der SimpaTec GmbH ist unser Antrieb und zur gleichen Zeit auch als Appell an unsere Kunden gerichtet: "Break your limits"! Es ist eine Aufforderung an Jeden von uns, Barrieren zu überwinden, über seine Grenzen hinaus zu denken, sich so neue Horizonte zu erobern, mögen sie auch noch so kühn erscheinen.
Definieren und verfolgen Sie Ihre neuen Ziele und Projekte mit SimpaTec!
Mit Kompetenz, Erfahrung, Ehrgeiz und dem Einsatz modernster Softwaretechnologien setzen wir gemeinsam mit Ihnen neue Standards bei der ganzheitlichen Entwicklung und Optimierung von Prozessen, Bauteilen und Werkzeugen. Wir begegnen jeder noch so komplexen Fragestellung mit wissenschaftlicher Expertise. Aufgrund unserer Marktstellung und internationalen Präsenz, sind wir immer über die neuesten Forschungsergebnisse und Entwicklungstrends informiert.
SimpaTec ist damit Ihr erster Ansprechpartner und mit Sicherheit der führende Berater, um leistungsfähige und hochwirksame Software- und Dienstleistungspakete zu bündeln. Von der Konstruktion mittels CAD über die Prozessoptimierung bis hin zur Lastfallanalyse mit impliziten oder expliziten CAE-Anwendungen in allen Fragen stehen unseren Kunden hervorragend ausgebildete Mitarbeiter an acht verschiedenen Standorten – in Aachen, Hamburg, Reutlingen, Weimar (Deutschland), Schlierbach (Österreich), Guebwiller (Frankreich), Bangkok (Thailand) sowie in den USA als kompetente Ansprechpartner zur Verfügung.
SimpaTec Simulation & Technology Consulting GmbH
Wurmbenden 15
52070 Aachen
Telefon: +49 (241) 565276-0
Telefax: +49 (241) 565276-99
http://www.simpatec.com
Manager PR & Social Media
Telefon: +49 (241) 565276-0
Fax: +49 (241) 565282-89
E-Mail: n.baxter@simpatec.com
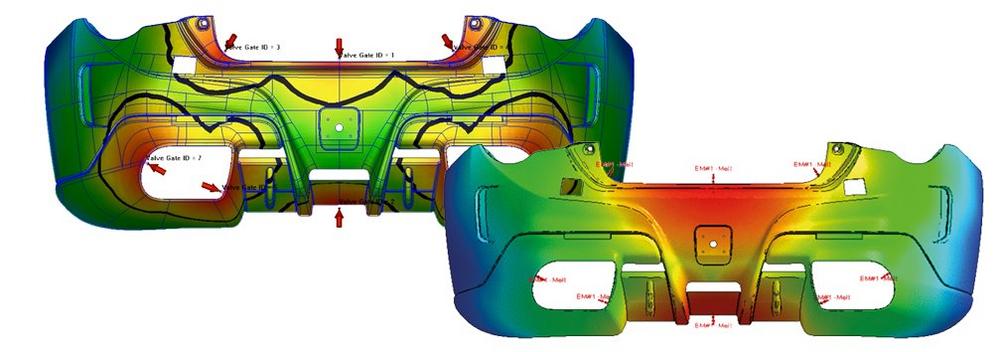
3D-Füllsimulation für jedermann
Der Moldex3D Viewer Advanced ermöglicht dem User, unter einer benutzerfreundlichen Oberfläche, den detaillierten Blick ins Innere der Kavität. Mittels realer 3D-Füllsimulationsergebnisse wird eine optimale Diskussionsgrundlage für weitere Entwicklungsschritte bis hin zur Optimierung der Herstellbarkeit des Bauteils erzielt. Diese Analysen können sowohl für Thermoplaste als auch für reaktive Kunststoffe durchgeführt werden.
Prüfen des Bauteildesigns und Bauteilfüllung
Wann entstehen die meisten Probleme bei der Herstellung von Spritzgussbauteilen? In der Bauteilentwicklung! Der Viewer Advanced steuert dem entgegen, in dem er über eine große Auswahl an Funktionen und Tools verfügt, um Bauteildesigns zu überprüfen, Bauteileigenschaften zu visualisieren und entsprechend vorliegender Analyseergebnisse zu optimieren. Mögliche Schwachstellen des Bauteils können so frühzeitig erkannt, analysiert und geeignete Gegenmaßnahmen eingeleitet werden. Mehrkosten durch Iterationen in Produkt-, Werkzeug- und Prozessoptimierung können so vermieden werden.
Blick in das Bauteil
Ein weiterer entscheidender Vorteil der Software ist, dass man nicht nur Ergebnisse der Bauteiloberfläche erhält, sondern einen detaillierten Blick ins Innere der Kavität werfen kann. Bauteilfehler wie, Bindenähte oder Lufteinschlüsse werden präzise dargestellt und „Tracer Partikel“ spielen eine wichtige Rolle bei der Beurteilung der Bindenahtqualität. Mittels sichtbarer Hotspots können Wandstärken und damit die Herstellbarkeit des Bauteils bereits in der frühen Entwicklungsphase optimiert werden.
Weitere Highlights über die der Moldex3D Viewer Advanced verfügt, sind u.a. die zusätzlichen Funktionen, die sowohl aussagekräftige Simulationen von Füllunterschieden aufzeigen als auch eine lückenlose Prozessüberwachung unterschiedlicher Paramater ermöglichen. Ferner erlaubt der integrierte Anguss-Wizard die Auswahl unterschiedlichster Angusstypen.
Interessiert an diesem absoluten Allrounder und EINSTEIGERPAKET?! Überzeugen Sie sich selbst wie die SimpaTec, durch Kombination qualitativ hochwertiger Simulation und kundennaher Beratungsdienstleistung, ein kompetenter Partner für die kunststoffverarbeitende Industrie sein kann und den Weg zur Produkt- und Prozessoptimierung möglichst kurz und effizient gestaltet.
SimpaTec Simulation & Technology Consulting GmbH
Wurmbenden 15
52070 Aachen
Telefon: +49 (241) 565276-0
Telefax: +49 (241) 565276-99
http://www.simpatec.com
E-Mail: s.paul@simpatec.com
Manager PR & Social Media
Telefon: +49 (241) 565276-0
Fax: +49 (241) 565282-89
E-Mail: n.baxter@simpatec.com
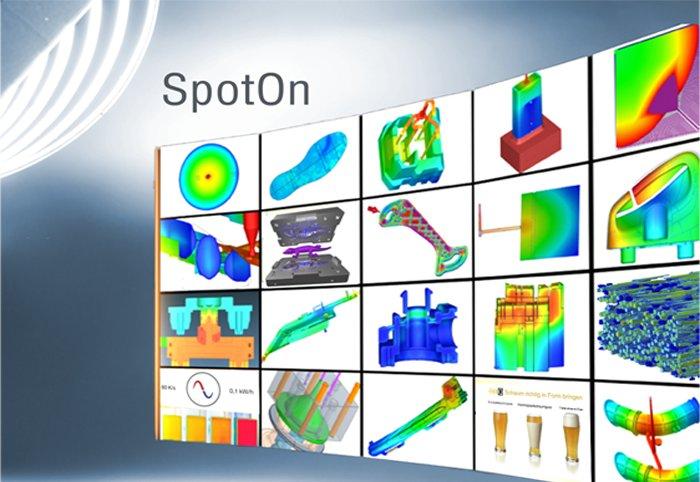
SpotOn & Action !! – SimpaTecs neue kostenfreie Veranstaltungsreihe …
Die erst kürzlich vorgestellte Veranstaltungsreihe erfreut sich bereits jetzt einer äußerst positive Gesamtresonanz. Verantwortlich für den Erfolg sind nicht nur die zahlreichen Teilnehmer, sondern auch die professionellen Referenten namhafter Unternehmen wie z.B. von der Contura MTC GmbH, Volume Graphics GmbH, HeiQ – Heitkamp Kunststofftechnik, die wertvolle, fundierte und technisch interessante ‚up-to-date‘ Informationen zu Themen wie "Konturnahe Kühlung", "Fasern" und "Schäumen" präsentierten.
Für Neugierige und Interessierte, die mehr über die neuesten Erkenntnisse, Ideen, aktuellem Fachwisse und über Potenziale und Perspektiven zukunftsweisender Technologien erfahren möchten, lohnt sich definitiv ein Blick in einen der kommenden SpotOn’s! Geplante zukünftige Themen sind u.a. "Bindenähte", "Sensorik für Werkzeugmaschinen", "Wasserinnnendruck", "Einfluss von Spritzgießmaschinen", "Optik", usw..
Der Zeit einen Schritt voraus zu sein und zu wissen, was morgen gefordert wird, ist unerlässlich. Die Erwartungen an Produkt- und Prozessmanagement in der Kunststoffindustrie ändern sich schnell und signifikant. Es gilt, mit Engagement neueste Forschungsergebnisse, Trends und Innovationen zu verfolgen, um neueste Entwicklungstendenzen frühzeitig zu erkennen und in die Weiterentwicklung von Produkten, Verfahren, Software und Dienstleistungen einfließen zu lassen.
SimpaTec lädt alle Personen ein, die sich für die ausgewählten Themen der digitalen, kostenlosen Veranstaltungsreihe interessieren. Bleiben Sie auf dem Laufenden und registrieren Sie sich für einen der SpotOns. Break your limits!
SimpaTec Simulation & Technology Consulting GmbH
Wurmbenden 15
52070 Aachen
Telefon: +49 (241) 565276-0
Telefax: +49 (241) 565276-99
http://www.simpatec.com
Manager PR & Social Media
Telefon: +49 (241) 565276-0
Fax: +49 (241) 565282-89
E-Mail: n.baxter@simpatec.com
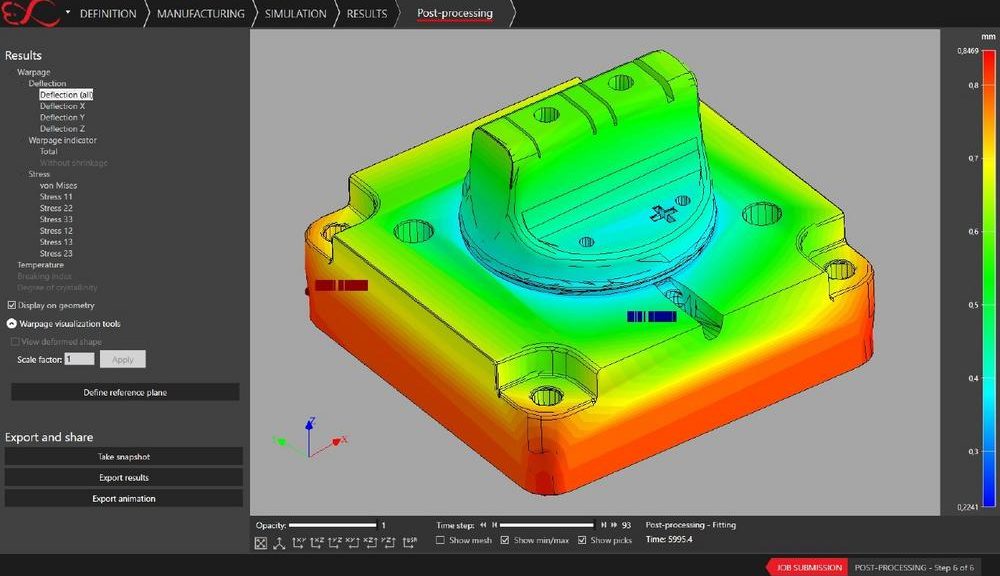
Berechnung von 3D gedruckten Werkzeugeinsätzen im Spritzguss
Mittels Digimat-AM existiert die erste Prozesssimulation im Bereich der Additiven Fertigung für Kunststoffbauteile. Dabei können verschiedene Additive Prozesse sowie unterschiedliche Materialien, wie verstärkte Composites, in der Simulation abgebildet werden. Die Verstärkung kann diverse Werkstoffe, wie u.a. Glas oder Carbon, in Form von Fasern oder Kugeln enthalten. Mit Hilfe der Analyse der Prozesssimulation werden virtuell die Thematiken der Eigenspannungen sowie die der Schwindung und des Verzuges dargestellt und deren Optimierung ermöglicht. Dementsprechend besteht numerisch die Möglichkeit der Maßhaltigkeit des Werkzeugeinsatzes im Vorfeld an das Werkzeug anzupassen.
Die Spritzgießsimulation umfasst nach heutigem Standard die Modellierung sowie Berücksichtigung von Werkzeugeinsätzen. Dabei spielt zum einen die Temperierung des Einsatzes und zum anderen die mechanische Beanspruchung während des Spritzgießprozesses eine maßgebliche Rolle. Mittels experimentellen Datensätzen erfolgt das Fitten der Materialmodelle für die rheologischen und mechanischen Materialeigenschaften. Aufgrund weiterer Module in der Spritzgießsimulation, findet die Wechselwirkung zwischen dem anliegenden Druck der Schmelze mit der Deformation des Werkzeugeinsatzes in der Simulation eine Berücksichtigung. Hierdurch können direkte Aussagen über das lineare mechanische Verhalten der Werkzeugeinsätze getroffen werden. Um die Aspekte der Mikrostruktur eines 3D gedruckten Werkzeugeinsatzes in der strukturmechanischen FEA einfließen zu lassen, erfolgt eine Kopplung mit einem mikromechanischen Softwaretool und einem gängigen Finite Elemente Solver.
Um verlässliche Aussagen zum Bauteilverhalten von 3D gedruckten Bauteilen zu erhalten, muss der jeweilige Herstellungsprozess in einer gekoppelten Berechnung mit einbezogen werden. Die prozessinduzierten Eigenschaften definieren die lokale Mikrostruktur, wodurch das Bauteil kein symmetrisches oder isotropes Verhalten, sondern ein komplexes anisotropes Verhalten über die Wandstärke und lokaler Position aufzeigt. Beginnend mit dem gewählten Prozess der Additiven Fertigung findet eine Festlegung der prozessinduzierten Mikrostruktur statt. Somit existiert bei einem Selektiven-Laser-Sinter (SLS)-Verfahren eine große Abhängigkeit der Festigkeit vom gewählten Druckwinkel. Anderseits ergeben sich mit einem Fused-Filament-Fabrication (FFF)-Verfahren Einsparpotential bei dem Gewicht. Mit einem intelligenten Design des Spritzgießbauteils, des Angusssystems oder auch der Temperaturführung kann zum einen der wirkende Druck bzw. Beanspruchung auf den Werkzeugeinsatz während des Spritzgießprozesses eine Verringerung erfahren oder zum anderen an lokalen Bereichen zu einer höheren mechanischen Belastung führen. Über die integrierten Exportschnittstellen wird z.B. die Weitergabe von Faserorientierungen, Drücken oder auch Temperaturen an die FEA gewährleistet.
Bei Einsatz der Kopplung mit der Mikromechanik sowie der nichtlinearen Strukturmechanik finden einerseits die prozessinduzierten Eigenschaften und anderseits das komplexe nichtlineare Materialverhalten in der Analyse des Bauteilverhaltens eine Berücksichtigung. Das komplexe Materialverhalten von Composites kann in mikromechanischen Softwaretools berechnet werden. Darüber hinaus existiert die Möglichkeit, eine digitale Materialkarte an experimentelle Daten zu kalibrieren. Eine weitere Besonderheit stellt die Versagensmodellierung dar. Hierbei wird das Materialversagen in Abhängigkeit der jeweiligen Phase (Matrix/Verstärkungsstoff) oder des Orientierungswinkels modelliert. Ebenso stellt die Modellierung von Porosität bei Verwendung eines FFF-Prozesses oder in Kombination mit einem Composite kein Hindernis dar. In den softwareeigenen Schnittstellentools lassen sich im Anschluss die Informationen aus dem Herstellungsprozess, der komplexen nichtlinearen Materialkarte mit dem strukturmechanischen Modell automatisiert koppeln. Ferner findet die Berechnung über den Solver und die Analyse im Post-Prozessor statt.
Schlussendlich kann eine gesamtheitliche Betrachtung der verwendeten Herstellungsprozesse, dem physikalischen Materialverhalten und der Bauteilperformance erfolgen. Im ersten Schritt der Analyse stehen die Einzelergebnisse für die Herstellbarkeit im Fokus und danach die gesamtheitlichen Ergebnisse für ein optimiertes Bauteilverhalten. Mit Hilfe der numerischen Berechnung besteht die Möglichkeit, stabile sowie robuste Prozesse für die Fertigung zu definieren sowie die gegenseitige Abhängigkeit zwischen Prozess, Materialverhalten und Bauteilverhalten aufzuzeigen.
SimpaTec bietet seit 2004 maßgeschneiderte innovative Methoden und Lösungskonzepte zur Entwicklung und Optimierung von Spritzgießkomponenten für jede Phase des Prozesses an. Überzeugen Sie sich selbst, wie die SimpaTec als Ihr Ansprechpartner und Berater für hochleistungsfähige Simulationssoftware und Dienstleistungspakete Sie unterstützen kann – auch bei der gesamtheitlichen Betrachtung zwischen Prozess-Simulation, nichtlineare, multiskalare Materialmodellierung und der Strukturmechanischen FEA.
SimpaTec GmbH – Break your limits. Challenge us.
Die Kernphilosophie der SimpaTec GmbH ist unser Antrieb und zur gleichen Zeit auch als Appell an unsere Kunden gerichtet:
"Break your limits"! Es ist eine Aufforderung an Jeden von uns, Barrieren zu überwinden, über seine Grenzen hinaus zu denken, sich so neue Horizonte zu erobern, mögen sie auch noch so kühn erscheinen.
Definieren und verfolgen Sie Ihre neuen Ziele und Projekte mit SimpaTec!
Mit Kompetenz, Erfahrung, Ehrgeiz und dem Einsatz modernster Softwaretechnologien setzen wir gemeinsam mit Ihnen neue Standards bei der ganzheitlichen Entwicklung und Optimierung von Prozessen, Bauteilen und Werkzeugen. Wir begegnen jeder noch so komplexen Fragestellung mit wissenschaftlicher Expertise. Aufgrund unserer Marktstellung und internationalen Präsenz, sind wir immer über die neuesten Forschungsergebnisse und Entwicklungstrends informiert.
SimpaTec ist damit Ihr erster Ansprechpartner und mit Sicherheit der führende Berater, um leistungsfähige und hochwirksame Software- und Dienstleistungspakete zu bündeln. Von der Konstruktion mittels CAD über die Prozessoptimierung bis hin zur Lastfallanalyse mit impliziten oder expliziten CAE-Anwendungen in allen Fragen stehen unseren Kunden hervorragend ausgebildete Mitarbeiter an acht verschiedenen Standorten – in Aachen, Hamburg, Reutlingen, Weimar (Deutschland), Linz (Österreich), Guebwiller (Frankreich), Bangkok (Thailand) sowie in den USA als kompetente Ansprechpartner zur Verfügung.
SimpaTec Simulation & Technology Consulting GmbH
Wurmbenden 15
52070 Aachen
Telefon: +49 (241) 565276-0
Telefax: +49 (241) 565276-99
http://www.simpatec.com
E-Mail: s.paul@simpatec.com
Manager PR & Social Media
Telefon: +49 (241) 565276-0
Fax: +49 (241) 565282-89
E-Mail: n.baxter@simpatec.com
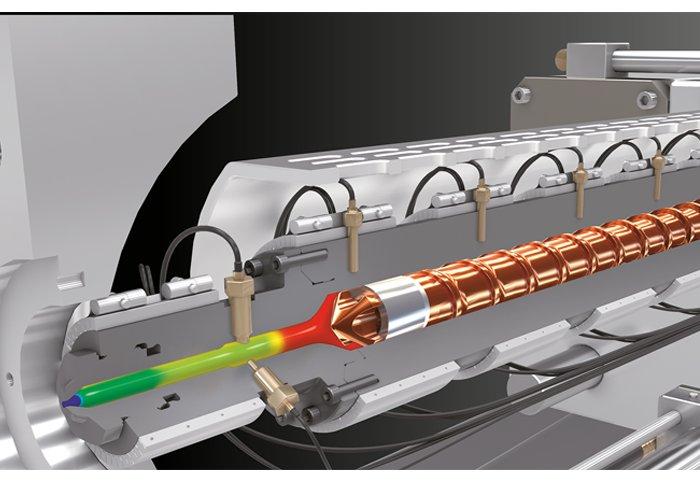
Moldex3D 2020 – „Geht über die Simulation hinaus“
Benutzerfreundlichkeit & Geschwindigkeit
Ein primäres Ziel der Entwicklungen war es, zeitgleich die bestehenden Simulationsmöglichkeiten kontinuierlich weiter zu entwickeln sowie parallel dazu, den Moldex3D Solver so zu optimieren, dass noch schnellere Berechnungszeiten erzielt werden. Durch eine Verfeinerung des Solvers innerhalb der Softwarearchitektur konnte dies tatsächlich realisiert werden. Eine erhebliche Leistungssteigerung ist die Folge, Anwender sparen bei Ihren Analysen nun – sage und schreibe – mehr als 20% der Berechnungszeit!
Mittels neuer Tools und Funktionalitäten im Bereich der Geometrie- und Netzreparatur wird die Bearbeitung von – sowohl Geometrie- als auch Netzproblemen – einfacher, bequemer und spart ebenfalls Zeit. Konstruktionsänderungen erfolgen noch schneller und garantieren mehr Effektivität.
Umfassende erweiterte Funktionalitäten
Die Industrie steht aufgrund der sich rasch ändernden Marktanforderungen, den Auswirkungen der allgemeinen Globalisierung, vor allem aber auch aufgrund der aktuellen Auswirkungen der Corona-Pandemie, vor gewaltigen Herausforderungen. Moldex3D bietet universale und zukunftsweisende Arbeitsmittel, mit denen Anwender bei Produktinnovationen und -entwicklung entscheidend wettbewerbsfähiger sein können. Im Bereich RTM bietet die neue Version deutliche Verbesserungen. So liegt beispielsweise bei der Simulation von 2D-Geweben die Vorhersage realistisch nah am tatsächlichen Verzug des Produkts. Einen weiteren bedeutenden Durchbruch gibt es im Bereich Chemisches Schäumen, die intensiven Entwicklungsschritte haben sich gelohnt – das Modul unterstützt nun die Analyse der Auflösung und Temperatur für das schäumende Gas sowie das Zusammenziehen von duroplastischen Materialien.
Intelligente Fertigung erfordert eine ‚smarte‘ Datenverwaltungsplattform (iSLM)
Der aktuelle Trend der intelligenten Fertigung erfordert automatisch ein Umdenken in Punkto Datenverwaltung und -archivierung – ein Wandel im Bereich Produktion ist hier unvermeidlich. Unabdingbar wird es sein, Unternehmen bei der Datensammlung und Zentralisierung des Datenmanagements zu unterstützen und aus diesem Prozess essentielle Werte abzuleiten, die die Arbeitseffizienz des gesamten Teams steigert! Moldex3D iSLM wurde entwickelt, um genau diesen Bedarf zu erfüllen.
iSLM ist eine intelligente und interaktive Cloud-basierte Datenverwaltungsplattform, die speziell für Unternehmen der Kunststofftechnik entwickelt wurde. Die Datenverwaltung umfasst u.a. die Größe von Modellmerkmalen, Anschnittgrößen, Anschnitttypen, Kühlsysteme, Abmusterungsparameter, CAE-Simulationsergebnisse uvam. Benutzer können die wichtigen und wertvollen Daten in der iSLM-Plattform während des gesamten Produktentwicklungslebenszyklus fortlaufend zentralisieren.
Die auf Werkzeugnummern basierte Speicherstruktur verknüpft und verfolgt auf einfache Weise eine Reihe von Daten und hilft nicht nur bei der Visualisierung der CAE-Simulationsergebnisse, sondern auch bei der Überprüfung der Testreihen vor Ort. Zusätzlich kann mit einer regelmäßigen Überprüfung der Informationen zum Werkzeugdesign in iSLM, die Qualität der gefertigten Bauteile überwacht werden.
Mit der Option, Zehntausende von Daten hochzuladen, kann iSLM die Teammitglieder in den beteiligten Abteilungen verwalten. Eine schnelle Kommunikation zwischen den Beteiligten ist gewährleistet und der Vergleich zwischen verschiedenen Designansätzen ist einfach und effizient.
„Mit Moldex3D 2020 wird die Entwicklung und Produktion von Bauteilen erheblich vereinfacht.“, unterstreicht Steffen Paul, Geschäftsführer und verantwortlicher Produktmanager der SimpaTec, die neuen Funktionalitäten und Weiterentwicklungen des Releases. „Die neue Version setzt einen Meilenstein, der im wahrsten Sinne des Wortes ‘über die Simulation hinausgeht‘. Die Verschickung an unsere Anwender ist primär vollendet. Wir freuen uns außerordentlich über erste Reaktionen, die uns zeigen, dass nicht nur der Name grundlegend Neues vermittelt, sondern Moldex3D 2020 genau das hält, was es verspricht.“
SimpaTec Simulation & Technology Consulting GmbH
Wurmbenden 15
52070 Aachen
Telefon: +49 (241) 565276-0
Telefax: +49 (241) 565276-99
http://www.simpatec.com
Manager PR & Social Media
Telefon: +49 (241) 565276-0
Fax: +49 (241) 565282-89
E-Mail: n.baxter@simpatec.com
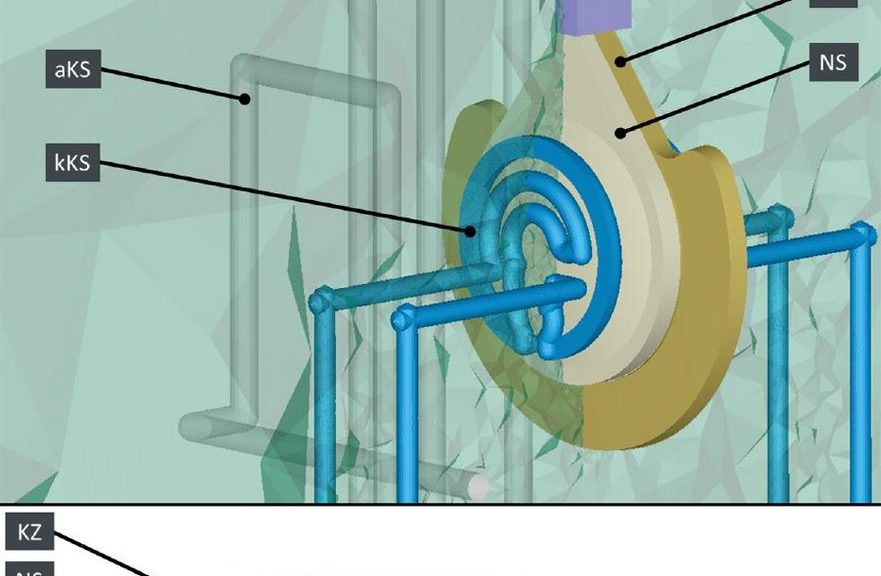
Mehr ist weniger
Einleitung
Nicht erst seit dem 17. Jahrhundert, in dem unter anderem die Laterna magica (die Zauberlaterne) entwickelt worden ist, spielen Optiken eine wichtige Rolle in dem Leben der Menschen [1]. Die ersten optischen Produkte, die von Menschen angefertigt worden sind, gehen noch deutlich weiter zurück in die Geschichte. So wurden in der damaligen Zeit im Wesentlichen Quarze geschliffen bzw. poliert, um Produkte mit gewünschten Eigenschaften zu erzielen.
In der heutigen Zeit ist der Alltag ohne optische Produkte kaum vorstellbar. Dazu zählen nicht nur die offensichtlichen Bauteile wie Brillen, Kameras und Projektoren. Viel mehr sind es auch Anwendungsbereiche der Messtechnik, der Fahrzeugtechnik etc., in denen diese Technologie eine tragende Rolle spielt. Das breite Anwendungsspektrum hat zur Folge, dass sich die mechanische Herstellung optischer Produkte stetig neuen Herausforderungen stellen muss und sich somit nicht nur das Fertigungsverfahren, sondern auch der Werkstoff Quarz mit der Frage nach Alternativen konfrontiert sieht. Bereits im Jahr 1933 brachte daher die Röhm & Haas AG ein Polymethylmethacrylat (PMMA) mit dem Markennamen Plexiglas auf dem Markt [2]. Gut sieben Jahre später entstand ein Produkt, das erstmals im Jahr 1636 von René Descartes dargestellt wurde [3] – der Vorläufer der Kontaktlinse. Entwickelt und realisiert wurde diese 1940 von Heinrich Wöhlk [4]. Es folgten eine ganze Reihe von Entwicklungen, doch das Beispiel der Kontaktlinse verdeutlicht, wie lange und wie sehr das Thema der Optik die Menschheit bereits begleitet. Einen entscheidenden, zukunftsträchtigen Schritt brachte letztlich der Beginn des Zusammenspiels von Kunststoff und dessen Einsatz bei der Herstellung von Produkten mit optischen Eigenschaften. So ermöglicht der Einsatz des Spritzgussverfahrens für die Kombination dieser beiden Komponenten – Kunststoff und Optik – die Produktion großer Stückzahlen mit reproduzierbaren Resultaten. Jedoch weist das Verfahren auch Herausforderungen wie ungleichmäßige Schwindung, Spannungen und Einfallstellen auf. Da im Vergleich zu technischen Produkten an Produkte mit optischen Eigenschaften erhöhte Anforderungen gestellt werden [5], kommt ein weiteres Herstellungsverfahren – das Spritzprägen – zur Produktion dieser Produkte in Frage. Durch die Kombination des Spritzgusses und des Fließpressens können nicht nur verfahrenstechnische (wie z. B. Fülldruck), sondern auch bauteilrelevante Eigenschaften optimiert werden [6]. Im Wesentlichen steht hier in Bezug auf die Bauteile die Homogenisierung sowohl von Material- wie auch von Bauteileigenschaften im Vordergrund.
Einerseits bietet das Spritzprägen gegenüber dem Spritzgussverfahren qualitativ bessere Bauteile mit optischen Eigenschaften, auf der anderen Seite fallen zum Teil nicht unerhebliche Kosten an. An dieser Stelle kommt das Thema der Prozesssimulation ins Spiel. Hier stehen nicht nur die Möglichkeit, den jeweiligen Prozess, wie auch bei technischen Bauteilen, zu abzubilden, sondern vor allem auch die Berechnung weiterführender Resultate, wie optischen Eigenschaften (z. B. Doppelbrechungen, Brechungsindex, Brechungsmuster, Retardation), im Vordergrund. Zur Verfügung steht ein Instrument nicht nur zur Optimierung der Herstellung von optischen Bauteilen, sondern vor allem auch zur Entscheidung, welcher Prozess für welches Produkt am besten und am wirtschaftlichsten geeignet ist.
Darstellung der Simulation
Die Prozesssimulation ist ein seit Jahren etabliertes Instrument, um – nicht nur im Rahmen von Troubleshooting – Erkenntnisse über real vorhandene Fehler zu erhalten. Vielmehr wird dieses Werkzeug im Rahmen der Entwicklung eingesetzt, um auf diesem Wege schon im Vorfeld potentielle Probleme zu erkennen und entsprechend zu verhindern. Ferner können alternative Prozesse, Materialen und selbst Verfahren simulativ evaluiert werden. Da allerdings die Prozesssimulation in vielen Fällen nur ein Teil der simulativen Entwicklungskette ist, gewinnt die Kopplung unterschiedlicher Berechnungsmethoden und -verfahren an immer mehr Bedeutung. So ist es in vielen Unternehmen durchaus üblich, die Prozesssimulation mit der strukturmechanischen Simulation zu koppeln, um so zusätzlich Daten wie die anisotropen Materialeigenschaften, Bindenähte etc. zu übertragen.
Auch zur Auslegung von optischen Produkten stehen derartige Kopplungsmethoden zur Verfügung. So kann aus Moldex3D unter anderem der Brechungsindex oder auch die Verformung nach Code V exportiert werden, auf diesem Weg erhält man aussagekräftigere Resultate, zum Beispiel hinsichtlich möglicher Abbildungsfehler. Dies gilt sowohl für den Prozess des Spritzgießens als auch des Spritzprägens.
Es ist festzuhalten, dass sich sowohl die Berechnung des Spritzprägens als auch die Berechnung von optischen Eigenschaften teilweise merklich gegenüber den Spritzgussberechnungen unterscheiden. Dazu zählt nicht nur die Prozesssteuerung, sondern für das Spritzprägen ebenfalls die Behandlung des Berechnungsmodells. Die Berechnung erfolgt in 3D und wird für beide Prozesse in die Schritte Füllphase/Prägephase/Nachdruckphase/Kühlphase unterteilt. Eine Besonderheit ergibt sich im Rahmen des Prägens. Um den Prägehub simulieren zu können, wird das Netz als Funktion der Zeit verformt. Somit verändert sich auch entsprechend der sogenannten Domain innerhalb der Berechnung. Oftmals werden die Kunststoffe mittels Viskosität, pvT-Verhaltens, Wärmeleitfähigkeit und spezifischer Wärmekapazität, Coefficient of Linear Thermal Expansion (CLTE), Querkontraktionszahl und E-Modul beschrieben. Um für beide Prozesse auch die spezifischen Resultate der optischen Eigenschaften zu erhalten, werden viskoelastischen Eigenschaften des Kunststoffes benötigt.
Auf diesem Wege können nicht nur Resultate, wie beispielsweise die Doppelbrechung oder auch Eigenspannungen, berechnet werden, sondern es kann ebenfalls zwischen thermisch- und fließ-induziert unterschieden werden.
Multilayer-Spritzgießen
Dickwandige Kunststoffoptiken, die zum Beispiel als Vorsatzoptiken zur definierten Lichtverteilung zum Einsatz kommen, können Wandstärken von bis zu 60 mm aufweisen.
Um die Qualität der Optik zu gewährleisten, können beim klassischen Spritzgießverfahren Zykluszeiten von mehr als 20 Minuten auftreten. Um diesem Effekt entgegenzuwirken und so eine Serienproduktion zu ermöglichen, ist das Multilayer-Spritzgießen für dickwandigen Linsen als Lösung entstanden. Das Mehrschichten-Spritzgießen ist an das Mehrkomponenten-Spritzgießen angelehnt. Beim Multilayer-Spritzgießen wird die fertige Optik in mehreren Einspritzvorgängen erzeugt und somit die Zykluszeit reduziert. Sowohl die Core-Back-Technik als auch die Transfertechnik und Drehtellertechnik, die schon etablierte Konzepte zur Herstellung von Mehrkomponentenbauteile sind, können im Multilayer-Spritzgießen eingesetzt werden. Des Weiteren kann ein konturnahes Temperiersystem und/oder eine dynamische Temperierstrategie zu einem gleichmäßigeren Abkühlen und somit zu geringen Eigenspannungen führen. Im Folgenden wird die Herstellung von optischen Linsen im Multilayer-Spritzgießen mit der Core-Back-Technik und deren Simulation erläutert.
Simulationsmodell und -ablauf
Die in der Dissertation von Röbig [7] verwendete Geometrie wird vom Institut für Kunststoffverarbeitung (IKV) in Industrie und Handwerk an der RWTH Aachen zur Verfügung gestellt. Simuliert wird eine zweischichtige, asphärische, bikonvexe Optik.
In Bild 1 ist auf der linken Seite eine Gesamtübersicht des Simulationsmodells dargestellt. Zu sehen sind das Werkzeug (WZ), das allgemeine Kühlsystem (KS), das konturnahe Kühlsystem (kKS), der Heißkanal (HK), der Kaltkanal (KK) und die Kavität (K). Auf der rechten Seite sind Vor- (VS) und Nachspritzling (NS) sowie die Kompressionszone (KZ) für das Spritzprägeverfahren abgebildet. Die Kompressionszone entfällt beim Spritzgießverfahren. Als Material wird ein Polymethylmethacrylat (PMMA) (Typ: Plexiglas® 7N, Hersteller: Evonik Performance Materials GmbH, Darmstadt) eingesetzt. Für die Herstellung dieser Formgeometrie wird ein Werkzeug mit Core-Back-Technik verwendet [8]. Dieses Werkzeugkonzept ermöglicht durch einen hydraulischen Kernrückzug Vor- und Nachspritzling in der gleichen Kavität herzustellen. Der Prägehub der Kompressionszone erfolgt über eine Prägerahmenkonstruktion und die Schließbewegung der Spritzgießmaschine.
Bei der Simulation des Spritzgießprozesses wird im ersten Schuss die Kavität des Vorspritzlings ausgefüllt. Erreicht dieser die zuvor bestimmten Entformungskriterien, wird der physikalische Zustand des Bauteils für den zweiten Schuss übertragen. Der schließseitige
Werkzeugkern wird zurückgezogen und somit der Kavitätsraum des Nachspritzlings freigegeben. Mit dem zweiten Schuss wird der Nachspritzling in Form gebracht. Beim Spritzprägeverfahren wird hier der Vorspritzling analog zum Spritzgießen erstellt und ebenso übertragen. Beim Füllen des Nachspritzlings fährt der Prägekern an einem zuvor bestimmten Füllvolumen mit definiertem Prägekraft- und Geschwindigkeitsprofil zu.
In Bild 2 (oben) ist ein Ausschnitt einer Füllstudie abgebildet, die für den Nachspritzling im Spritzgießverfahren am IKV durchgeführt wurde. Die zugehörige, von SimpaTec ausgeführte, Simulation ist in Bild 2 (unten) dargestellt. In den drei ausgewählten Zeitschritten (t1 – t3) ist deutlich zu erkennen, dass die simulierte Fließfront im Vergleich zur realen Fließfront gut abgebildet wird.
Darstellung und Vergleich der Simulationsergebnisse
In Bild 3 und Bild 4 sind ausgewählte Ergebnisse der Spritzgieß- und Spritzprägesimulationen gegenübergestellt.
Die Druckverteilung am Ende der Nachdruckphase für die Spritzgießsimulation ist auf der linken Seite, die Druckverteilung nach der Prägephase der Spritzprägesimulation auf der rechten Seite von Bild 3 abgebildet. Deutlich zu erkennen ist der ausgeprägte Druckgradient ausgehend vom Anspritzpunkt beim Spritzgießen, während die simulierte Linse aus dem Spritzprägeverfahren eine homogenere Druckverteilung an den optischen Funktionsflächen aufweist.
In Bild 4 sind die lokalen fließ-induzierten Eigenspannungen in XX-Richtung anhand von Falschfarbendiagrammen veranschaulicht. Analog zu den Druckergebnissen sind auch an dieser Stelle deutliche Unterschiede zwischen den simulierten Linsen sichtbar, die im Spritzgießverfahren (links) und Spritzprägeverfahren (rechts) berechnet wurden. Im Gegensatz zur spritzgegossenen Linse zeichnet sich die spritzgeprägte Linse durch einen geringeren Eigenspannungsgradienten aus, woraus bessere optische Eigenschaften resultieren.
Die fließ- und thermisch-induzierten Brechungsmuster sowie die Überlagerung beider Effekte von der spritzgegossenen, simulierten Linse sind beispielhaft in Bild 5 abgebildet. Diese Simulationsergebnisse können unter Berücksichtigung realer, polarisationsoptischer Aufnahmen zur Fehleranalytik im Rahmen der Qualitätssicherung herangezogen werden. Durch die Trennung der fließ- und thermisch induzierten Brechungsmuster lassen ferner eine gezielte Ursachenanalyse zu.
Fazit
Spritzgießen vs. Spritzprägen? Konturnahe Temperierung vs. konventionelle Temperierung? Dies sind nur zwei aus einer ganzen Bandbreite von Fragen, die mittels einer simulationstechnischen Berechnung im Vorfeld beantwortet werden können. Sicherlich bietet auch die „klassische“ Spritzgusssimulation schon eine ganze Reihe von Antworten. Doch zeigen die dargestellten Kopplungsmethoden, dass die Möglichkeiten mittlerweile deutlich weiter gehen, um letztendlich ein im Vorfeld verbessertes Produkt bei optimalen Prozessbedingungen zu fertigen, unter Berücksichtigung sowohl von technischen, als auch von wirtschaftlichen Aspekten.
SimpaTec Simulation & Technology Consulting GmbH
Wurmbenden 15
52070 Aachen
Telefon: +49 (241) 565276-0
Telefax: +49 (241) 565276-99
http://www.simpatec.com
Manager PR & Social Media
Telefon: +49 (241) 565276-0
Fax: +49 (241) 565282-89
E-Mail: n.baxter@simpatec.com
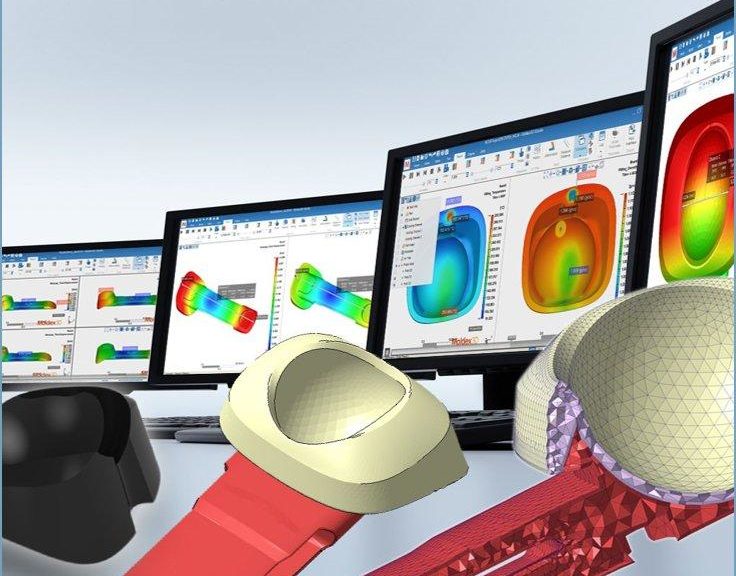
Eine gute Simulation beginnt mit der Füllung – VOLLE FUNKTIONALITÄT von Moldex3D bei Erwerb eines Basismoduls!
Um die gesamte Palette von Moldex3D, dem führenden 3D-CAE-Softwarepaket zur Analyse, Auslegung und Optimierung des Bauteils, Werkzeugs und Prozesses, aufzuzeigen, erhält man ab sofort bei Erwerb eines Einsteiger-Basismoduls bis zum Jahresende die vollständige Funktionalität des gesamten CAE-Paketes (inkl. Nachdruck, Temperierung und Verzug u.v.a.m.) als Teststellung kostenfrei. Somit erhält der Anwender die Chance, das System ausführlich und rundum zu testen. Am Jahresende hat man die Option zu entscheiden, ob auf das vollständige Simulationspaket gewechselt oder das Basismodul weitergenutzt wird.
Moldex3D
CoreTech System (Moldex3D) Co., Ltd. entwickelt und erweitert das professionelle CAE-Analysesoftwarepaket ‘Moldex’ für die Kunststoffspritzguss-Industrie seit 1995 stetig. Die aktuelle Produktversion Moldex3D 2020 ist marktführend. CoreTech bietet innovative Technologien, die Anwender unterstützt, Probleme bei der Konstruktion bis hin zur Produktentwicklung zu lösen, Werkzeuge zu optimieren, Markteinführungszeiten zu minimieren und ROI-Kennzahlen zu maximieren.
Weitere Informationen finden Sie bitte unter www.moldex3d.com
Die Kernphilosophie der SimpaTec GmbH ist unser Antrieb und zur gleichen Zeit auch als Appell an unsere Kunden gerichtet: "Break your limits"!
Es ist vielmehr eine Aufforderung an Jeden von uns, Barrieren zu überwinden, über seine Grenzen hinaus zu denken, um sich so neue Horizonte zu erobern, mögen sie noch so kühn erscheinen.
Definieren und verfolgen Sie Ihre neuen Ziele und Projekte mit SimpaTec!
Mit Kompetenz, Erfahrung, Ehrgeiz und dem Einsatz modernster Softwaretechnologien setzen wir gemeinsam mit Ihnen neue Standards bei der ganzheitlichen Entwicklung und Optimierung von Prozessen, Bauteilen und Werkzeugen.
Wir begegnen jeder noch so komplexen Fragestellung mit wissenschaftlicher Expertise. Aufgrund unserer Marktstellung und internationalen Präsenz, sind wir immer über die neuesten Forschungsergebnisse und Entwicklungstrends informiert.
SimpaTec ist damit Ihr erster Ansprechpartner und mit Sicherheit der führende Berater, um leistungsfähige und hoch wirksame Software- und Dienstleistungspakete zu bündeln. Von der Konstruktion mittels CAD über die Prozessoptimierung bis hin zur Lastfallanalyse mit impliziten oder expliziten CAE-Anwendungen in allen Fragen stehen unseren Kunden hervorragend ausgebildete Mitarbeiter an acht verschiedenen Standorten, Aachen, Reutlingen, Weimar, Hamburg sowie in Linz (Österreich), Guebwiller (Frankreich), Bangkok (Thailand) und USA als kompetente Ansprechpartner zur Verfügung.
SimpaTec Simulation & Technology Consulting GmbH
Wurmbenden 15
52070 Aachen
Telefon: +49 (241) 565276-0
Telefax: +49 (241) 565276-99
http://www.simpatec.com
Manager PR & Social Media
Telefon: +49 (241) 565276-0
Fax: +49 (241) 565282-89
E-Mail: n.baxter@simpatec.com
E-Mail: c.hinse@simpatec.com