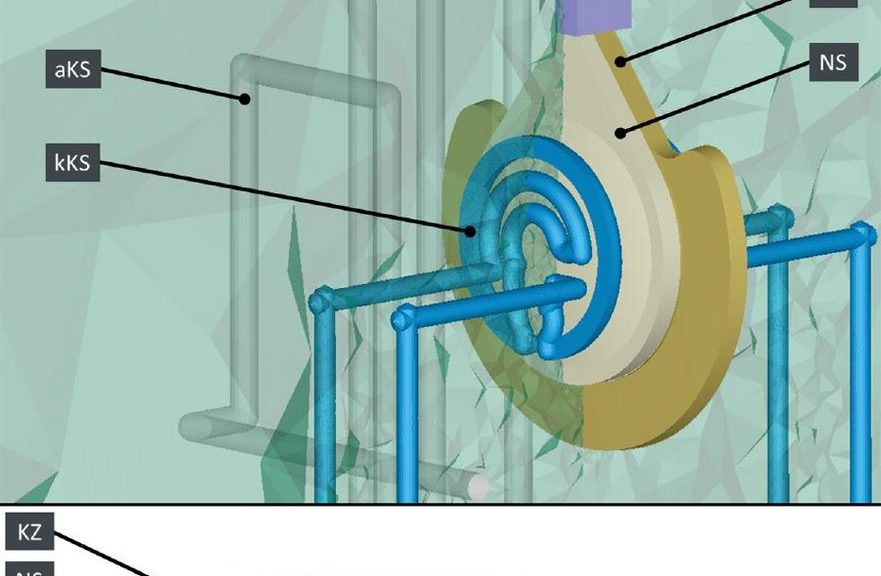
Mehr ist weniger
Einleitung
Nicht erst seit dem 17. Jahrhundert, in dem unter anderem die Laterna magica (die Zauberlaterne) entwickelt worden ist, spielen Optiken eine wichtige Rolle in dem Leben der Menschen [1]. Die ersten optischen Produkte, die von Menschen angefertigt worden sind, gehen noch deutlich weiter zurück in die Geschichte. So wurden in der damaligen Zeit im Wesentlichen Quarze geschliffen bzw. poliert, um Produkte mit gewünschten Eigenschaften zu erzielen.
In der heutigen Zeit ist der Alltag ohne optische Produkte kaum vorstellbar. Dazu zählen nicht nur die offensichtlichen Bauteile wie Brillen, Kameras und Projektoren. Viel mehr sind es auch Anwendungsbereiche der Messtechnik, der Fahrzeugtechnik etc., in denen diese Technologie eine tragende Rolle spielt. Das breite Anwendungsspektrum hat zur Folge, dass sich die mechanische Herstellung optischer Produkte stetig neuen Herausforderungen stellen muss und sich somit nicht nur das Fertigungsverfahren, sondern auch der Werkstoff Quarz mit der Frage nach Alternativen konfrontiert sieht. Bereits im Jahr 1933 brachte daher die Röhm & Haas AG ein Polymethylmethacrylat (PMMA) mit dem Markennamen Plexiglas auf dem Markt [2]. Gut sieben Jahre später entstand ein Produkt, das erstmals im Jahr 1636 von René Descartes dargestellt wurde [3] – der Vorläufer der Kontaktlinse. Entwickelt und realisiert wurde diese 1940 von Heinrich Wöhlk [4]. Es folgten eine ganze Reihe von Entwicklungen, doch das Beispiel der Kontaktlinse verdeutlicht, wie lange und wie sehr das Thema der Optik die Menschheit bereits begleitet. Einen entscheidenden, zukunftsträchtigen Schritt brachte letztlich der Beginn des Zusammenspiels von Kunststoff und dessen Einsatz bei der Herstellung von Produkten mit optischen Eigenschaften. So ermöglicht der Einsatz des Spritzgussverfahrens für die Kombination dieser beiden Komponenten – Kunststoff und Optik – die Produktion großer Stückzahlen mit reproduzierbaren Resultaten. Jedoch weist das Verfahren auch Herausforderungen wie ungleichmäßige Schwindung, Spannungen und Einfallstellen auf. Da im Vergleich zu technischen Produkten an Produkte mit optischen Eigenschaften erhöhte Anforderungen gestellt werden [5], kommt ein weiteres Herstellungsverfahren – das Spritzprägen – zur Produktion dieser Produkte in Frage. Durch die Kombination des Spritzgusses und des Fließpressens können nicht nur verfahrenstechnische (wie z. B. Fülldruck), sondern auch bauteilrelevante Eigenschaften optimiert werden [6]. Im Wesentlichen steht hier in Bezug auf die Bauteile die Homogenisierung sowohl von Material- wie auch von Bauteileigenschaften im Vordergrund.
Einerseits bietet das Spritzprägen gegenüber dem Spritzgussverfahren qualitativ bessere Bauteile mit optischen Eigenschaften, auf der anderen Seite fallen zum Teil nicht unerhebliche Kosten an. An dieser Stelle kommt das Thema der Prozesssimulation ins Spiel. Hier stehen nicht nur die Möglichkeit, den jeweiligen Prozess, wie auch bei technischen Bauteilen, zu abzubilden, sondern vor allem auch die Berechnung weiterführender Resultate, wie optischen Eigenschaften (z. B. Doppelbrechungen, Brechungsindex, Brechungsmuster, Retardation), im Vordergrund. Zur Verfügung steht ein Instrument nicht nur zur Optimierung der Herstellung von optischen Bauteilen, sondern vor allem auch zur Entscheidung, welcher Prozess für welches Produkt am besten und am wirtschaftlichsten geeignet ist.
Darstellung der Simulation
Die Prozesssimulation ist ein seit Jahren etabliertes Instrument, um – nicht nur im Rahmen von Troubleshooting – Erkenntnisse über real vorhandene Fehler zu erhalten. Vielmehr wird dieses Werkzeug im Rahmen der Entwicklung eingesetzt, um auf diesem Wege schon im Vorfeld potentielle Probleme zu erkennen und entsprechend zu verhindern. Ferner können alternative Prozesse, Materialen und selbst Verfahren simulativ evaluiert werden. Da allerdings die Prozesssimulation in vielen Fällen nur ein Teil der simulativen Entwicklungskette ist, gewinnt die Kopplung unterschiedlicher Berechnungsmethoden und -verfahren an immer mehr Bedeutung. So ist es in vielen Unternehmen durchaus üblich, die Prozesssimulation mit der strukturmechanischen Simulation zu koppeln, um so zusätzlich Daten wie die anisotropen Materialeigenschaften, Bindenähte etc. zu übertragen.
Auch zur Auslegung von optischen Produkten stehen derartige Kopplungsmethoden zur Verfügung. So kann aus Moldex3D unter anderem der Brechungsindex oder auch die Verformung nach Code V exportiert werden, auf diesem Weg erhält man aussagekräftigere Resultate, zum Beispiel hinsichtlich möglicher Abbildungsfehler. Dies gilt sowohl für den Prozess des Spritzgießens als auch des Spritzprägens.
Es ist festzuhalten, dass sich sowohl die Berechnung des Spritzprägens als auch die Berechnung von optischen Eigenschaften teilweise merklich gegenüber den Spritzgussberechnungen unterscheiden. Dazu zählt nicht nur die Prozesssteuerung, sondern für das Spritzprägen ebenfalls die Behandlung des Berechnungsmodells. Die Berechnung erfolgt in 3D und wird für beide Prozesse in die Schritte Füllphase/Prägephase/Nachdruckphase/Kühlphase unterteilt. Eine Besonderheit ergibt sich im Rahmen des Prägens. Um den Prägehub simulieren zu können, wird das Netz als Funktion der Zeit verformt. Somit verändert sich auch entsprechend der sogenannten Domain innerhalb der Berechnung. Oftmals werden die Kunststoffe mittels Viskosität, pvT-Verhaltens, Wärmeleitfähigkeit und spezifischer Wärmekapazität, Coefficient of Linear Thermal Expansion (CLTE), Querkontraktionszahl und E-Modul beschrieben. Um für beide Prozesse auch die spezifischen Resultate der optischen Eigenschaften zu erhalten, werden viskoelastischen Eigenschaften des Kunststoffes benötigt.
Auf diesem Wege können nicht nur Resultate, wie beispielsweise die Doppelbrechung oder auch Eigenspannungen, berechnet werden, sondern es kann ebenfalls zwischen thermisch- und fließ-induziert unterschieden werden.
Multilayer-Spritzgießen
Dickwandige Kunststoffoptiken, die zum Beispiel als Vorsatzoptiken zur definierten Lichtverteilung zum Einsatz kommen, können Wandstärken von bis zu 60 mm aufweisen.
Um die Qualität der Optik zu gewährleisten, können beim klassischen Spritzgießverfahren Zykluszeiten von mehr als 20 Minuten auftreten. Um diesem Effekt entgegenzuwirken und so eine Serienproduktion zu ermöglichen, ist das Multilayer-Spritzgießen für dickwandigen Linsen als Lösung entstanden. Das Mehrschichten-Spritzgießen ist an das Mehrkomponenten-Spritzgießen angelehnt. Beim Multilayer-Spritzgießen wird die fertige Optik in mehreren Einspritzvorgängen erzeugt und somit die Zykluszeit reduziert. Sowohl die Core-Back-Technik als auch die Transfertechnik und Drehtellertechnik, die schon etablierte Konzepte zur Herstellung von Mehrkomponentenbauteile sind, können im Multilayer-Spritzgießen eingesetzt werden. Des Weiteren kann ein konturnahes Temperiersystem und/oder eine dynamische Temperierstrategie zu einem gleichmäßigeren Abkühlen und somit zu geringen Eigenspannungen führen. Im Folgenden wird die Herstellung von optischen Linsen im Multilayer-Spritzgießen mit der Core-Back-Technik und deren Simulation erläutert.
Simulationsmodell und -ablauf
Die in der Dissertation von Röbig [7] verwendete Geometrie wird vom Institut für Kunststoffverarbeitung (IKV) in Industrie und Handwerk an der RWTH Aachen zur Verfügung gestellt. Simuliert wird eine zweischichtige, asphärische, bikonvexe Optik.
In Bild 1 ist auf der linken Seite eine Gesamtübersicht des Simulationsmodells dargestellt. Zu sehen sind das Werkzeug (WZ), das allgemeine Kühlsystem (KS), das konturnahe Kühlsystem (kKS), der Heißkanal (HK), der Kaltkanal (KK) und die Kavität (K). Auf der rechten Seite sind Vor- (VS) und Nachspritzling (NS) sowie die Kompressionszone (KZ) für das Spritzprägeverfahren abgebildet. Die Kompressionszone entfällt beim Spritzgießverfahren. Als Material wird ein Polymethylmethacrylat (PMMA) (Typ: Plexiglas® 7N, Hersteller: Evonik Performance Materials GmbH, Darmstadt) eingesetzt. Für die Herstellung dieser Formgeometrie wird ein Werkzeug mit Core-Back-Technik verwendet [8]. Dieses Werkzeugkonzept ermöglicht durch einen hydraulischen Kernrückzug Vor- und Nachspritzling in der gleichen Kavität herzustellen. Der Prägehub der Kompressionszone erfolgt über eine Prägerahmenkonstruktion und die Schließbewegung der Spritzgießmaschine.
Bei der Simulation des Spritzgießprozesses wird im ersten Schuss die Kavität des Vorspritzlings ausgefüllt. Erreicht dieser die zuvor bestimmten Entformungskriterien, wird der physikalische Zustand des Bauteils für den zweiten Schuss übertragen. Der schließseitige
Werkzeugkern wird zurückgezogen und somit der Kavitätsraum des Nachspritzlings freigegeben. Mit dem zweiten Schuss wird der Nachspritzling in Form gebracht. Beim Spritzprägeverfahren wird hier der Vorspritzling analog zum Spritzgießen erstellt und ebenso übertragen. Beim Füllen des Nachspritzlings fährt der Prägekern an einem zuvor bestimmten Füllvolumen mit definiertem Prägekraft- und Geschwindigkeitsprofil zu.
In Bild 2 (oben) ist ein Ausschnitt einer Füllstudie abgebildet, die für den Nachspritzling im Spritzgießverfahren am IKV durchgeführt wurde. Die zugehörige, von SimpaTec ausgeführte, Simulation ist in Bild 2 (unten) dargestellt. In den drei ausgewählten Zeitschritten (t1 – t3) ist deutlich zu erkennen, dass die simulierte Fließfront im Vergleich zur realen Fließfront gut abgebildet wird.
Darstellung und Vergleich der Simulationsergebnisse
In Bild 3 und Bild 4 sind ausgewählte Ergebnisse der Spritzgieß- und Spritzprägesimulationen gegenübergestellt.
Die Druckverteilung am Ende der Nachdruckphase für die Spritzgießsimulation ist auf der linken Seite, die Druckverteilung nach der Prägephase der Spritzprägesimulation auf der rechten Seite von Bild 3 abgebildet. Deutlich zu erkennen ist der ausgeprägte Druckgradient ausgehend vom Anspritzpunkt beim Spritzgießen, während die simulierte Linse aus dem Spritzprägeverfahren eine homogenere Druckverteilung an den optischen Funktionsflächen aufweist.
In Bild 4 sind die lokalen fließ-induzierten Eigenspannungen in XX-Richtung anhand von Falschfarbendiagrammen veranschaulicht. Analog zu den Druckergebnissen sind auch an dieser Stelle deutliche Unterschiede zwischen den simulierten Linsen sichtbar, die im Spritzgießverfahren (links) und Spritzprägeverfahren (rechts) berechnet wurden. Im Gegensatz zur spritzgegossenen Linse zeichnet sich die spritzgeprägte Linse durch einen geringeren Eigenspannungsgradienten aus, woraus bessere optische Eigenschaften resultieren.
Die fließ- und thermisch-induzierten Brechungsmuster sowie die Überlagerung beider Effekte von der spritzgegossenen, simulierten Linse sind beispielhaft in Bild 5 abgebildet. Diese Simulationsergebnisse können unter Berücksichtigung realer, polarisationsoptischer Aufnahmen zur Fehleranalytik im Rahmen der Qualitätssicherung herangezogen werden. Durch die Trennung der fließ- und thermisch induzierten Brechungsmuster lassen ferner eine gezielte Ursachenanalyse zu.
Fazit
Spritzgießen vs. Spritzprägen? Konturnahe Temperierung vs. konventionelle Temperierung? Dies sind nur zwei aus einer ganzen Bandbreite von Fragen, die mittels einer simulationstechnischen Berechnung im Vorfeld beantwortet werden können. Sicherlich bietet auch die „klassische“ Spritzgusssimulation schon eine ganze Reihe von Antworten. Doch zeigen die dargestellten Kopplungsmethoden, dass die Möglichkeiten mittlerweile deutlich weiter gehen, um letztendlich ein im Vorfeld verbessertes Produkt bei optimalen Prozessbedingungen zu fertigen, unter Berücksichtigung sowohl von technischen, als auch von wirtschaftlichen Aspekten.
SimpaTec Simulation & Technology Consulting GmbH
Wurmbenden 15
52070 Aachen
Telefon: +49 (241) 565276-0
Telefax: +49 (241) 565276-99
http://www.simpatec.com
Manager PR & Social Media
Telefon: +49 (241) 565276-0
Fax: +49 (241) 565282-89
E-Mail: n.baxter@simpatec.com